Companies need to specify materials and designs to prevent environmentally induced cracking, as it can halt production and lead to loss of containment of hydrocarbons, raising safety and environmental risks and potentially resulting in huge costs and loss of license to operate. Trends such as subsea tie-backs to maximize hydrocarbon recovery in existing fields, renewed interest in developing deepwater fields, and oil and gas production under HPHT and/or sour (high H2S) conditions, are growing. Within subsea projects, Environmentally Assisted Cracking (EIC) poses a risk for all equipment: pipelines, Xmas trees, valves, pumps and manifolds.
Greater understanding of how the chemistry and physics of operating environments lead to cracking in materials is improving procurement in oil and gas industries. Models developed from empirical information, failures, testing and other input are enabling the right choice first time when assessing options for materials used for equipment, pipelines and structures including those offshore and subsea. The aim is to prevent environmentally induced cracking.
What causes environmentally assisted cracking?
Environmentally assisted cracking progressively weakens a material’s resistance to tensile stress, so that it may suddenly fail with no previous visible warning. It is usually caused due to the interaction of multiple factors such as high pressure (HP); high temperature (HT); high concentrations of hydrogen sulphide (H2S); and, microbially induced corrosion (MIC). Also, many structures have cathodic protection which can result in the production of hydrogen that can cause a form of EAC called hydrogen-induced stress cracking (HISC) of materials.
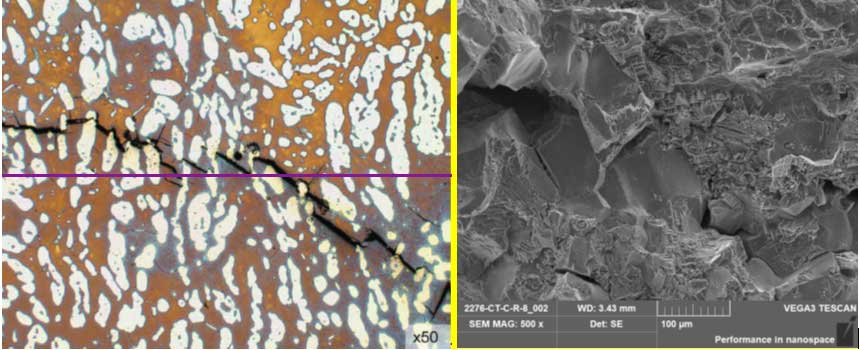
Environmentally assisted cracking.
Choosing the right materials early to prevent cracking
Customers typically consult our experts even before the front-end engineering design (FEED) phase, allowing us to identify design pinch points when materials are being chosen. We can then advise them on the risk associated with the design options being considered.
To do this, we call on our extensive database of materials performance in various environments; empirical models; in-depth knowledge of published research; and, the experience of other operators.
As an example, DNV has developed an approach to evaluate material selection for wells and downhole equipment taking into account site-specific data.
With world-leading expertise in testing materials resistance to environmentally induced cracking (HISC, SCC, etc.), we have developed models for cracking mechanisms and guidelines on how to avoid this. Our materials and component testing laboratories in Norway (Bergen, Høvik), Singapore, UK and US can simulate some of the world’s most complex field conditions. In realistic corrosion environments, we test both metallic and non-metallic materials, with specialities in harsh environments such as H2S sour service testing, and HPHT.
We can share learnings within and between industries, Deep domain expertise and knowledge coupled with data analytics are valuable in providing materials selection solutions. Being involved pre-FEED means there are very few subsequent failures due to environmentally assisted cracking.
What standards apply to materials in sour environments?
Knowing what does and could go wrong also allows us to advise on applying relevant standards such as ISO 15156/NACE MR 0175 for materials that will be exposed in a sour environment and need to be pre-qualified or qualified for the purpose. Oil and gas pipelines and processing plants are among assets that may need to operate in sour-service containing environments.
We conduct research1,2 into EAC, and run joint industry projects (JIPs) with customers to develop new solutions, standards and recommended practices. Current examples include JIPs on the performance of pipeline steels in high concentration H2S environments. We provided input to DNV's Standard DNV-ST-F101 Submarine pipeline systems.
Reference:
1. R. Thodla, C. Holtam, R. Saraswat, Journal of Pressure Vessel Technology 142, 3 (2020)2. R. Thodla, N. Sridhar, H. Amaya, B. Fahimi, C. Taylor, CORROSION 76, 3 (2020): p. 299-311