Zero avoidable waste by 2050: Exploring the emerging market of end-of-life tyre recycling
Tyres serve a crucial function across diverse transportation modes, including road and aviation. However, they have finite usable lifespans. Whilst applications vary, tyres typically consist of rubber, carbon black, steel inserts, oil, and vulcanizing agents, as well as synthetic yarns and textiles.
The usage of tyres worldwide is expected to increase in line with the growth in vehicle ownership, which, as detailed within the DNV’s Energy Transition Outlook 2023 (ETO), will stabilize at around 3.4 billion vehicles in the mid-2040s. The increase is primarily driven by growth in car ownership in Asia Pacific. Estimates suggest that there will be as many as 5 billion waste tyres in landfills and stockpiles globally by 2030.1
When tyres are no longer suitable to perform their intended use, they are discarded and are considered ‘End of Life Tyres’ (ELTs): a waste product. The number of ELTs is anticipated to increase faster than the growth in vehicle ownership due to the transition from petroleum-based vehicles to electric vehicles (EVs). The increase in market share of passenger EVs from 8% today to 96% by 2050, as projected by the ETO, will spur a more challenging landscape due to increased weight and acceleration capabilities of EVs, shortening tyre lifespans. This trend is countered by the transition towards public transport, adopted initially in developed countries, because of Net Zero policies, and subsequently globally in line with the energy transition.
Historically, ELTs have been landfilled or burned to provide a low-grade heat source, e.g. for cement kilns, with low efficiency and dangerous or unusable by-products. Alternatively, ELTs are shredded and downcycled for use in construction or turfing applications. However, environmental laws limiting emissions and concerns around chemical leaching have catalysed recycling requirements and policy. With an increasing drive towards circularity and deriving value from waste, such as by the goals defined in the EU Circular Economy Action Plan,2 a market for re-processing ELTs has emerged.
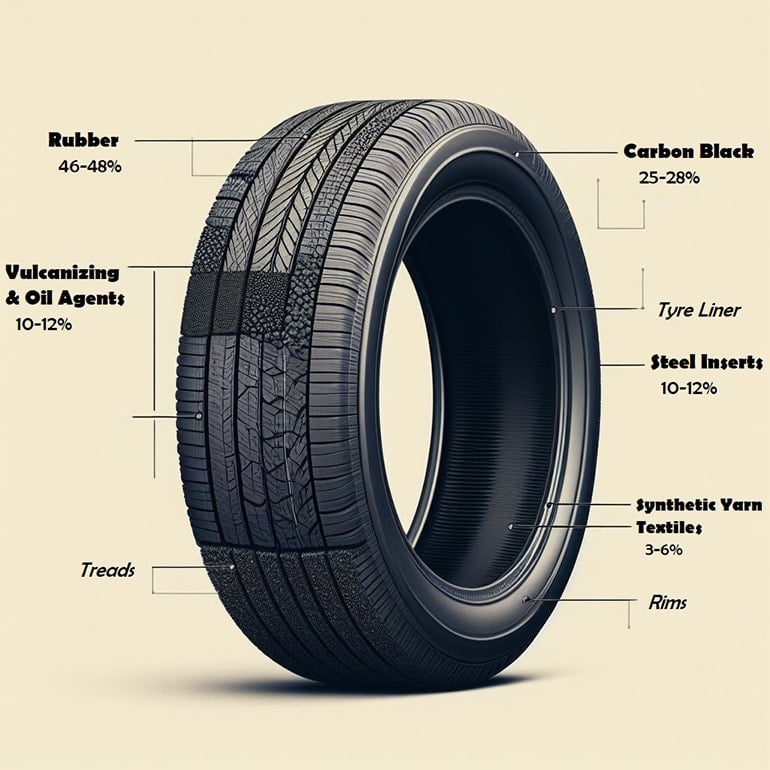
Figure 1: Depicting the typical constituents of a standard road tyre [Dall-E 3]
Conventional closed-loop recovery: Tyre pyrolysis oils, recovered carbon black, scrap steel, and gas
Once collected and sorted, discarded ELTs are run through a streamlined process of material recovery that typically involves metal stripping/debeading, granulation/shredding, crumbing and devulcanization or pyrolysis. Regardless of the process, the output is three distinct products: tyre pyrolysis oils (TPOs), recovered carbon black (rCB), and scrap steel – along with gas (~40-30-20-10 weight%). The scrap steel is sold to producers via mature supply chains. TPOs and rCB are where the opportunity is being developed.
![Artist rendition of historical tyre recycling operations [Dall-E 3]](/contentassets/72bbbea5d28e49f5aa074d8d810b9eee/tyre-recycling-2.jpg?mode=crop&width=864)
Recovered carbon blacks (rCBs)
Carbon Black is used as a reinforcing agent in rubber products for improvements in physical properties e.g., tensile strength or elasticity, durability, and aesthetics, imparting the black colour to tyres. The pyrolysis component of the process exposes the shredded ELTs to high temperatures in the absence of air, causing the rubber to decompose into a mix of hydrocarbon gases. These gases are drawn off, leaving a carbon black rich residue. Virgin Carbon Blacks (vCB) are produced via a high temperature pyrolysis process of fossil-fuel-derived decant oils, with an inherently large energy footprint, and typically contain more than 95% pure carbon. Conversely, rCB can contain up to 40% of inorganics or carbonaceous residues, with the remaining content composed of a blend of the original vCB grades, derived from parts of the original tyre with differing target requirements. The consequence of this blend is poorer reinforcing potential and variation in imparted properties, allowing for only partial replacement of vCB in tyre production.
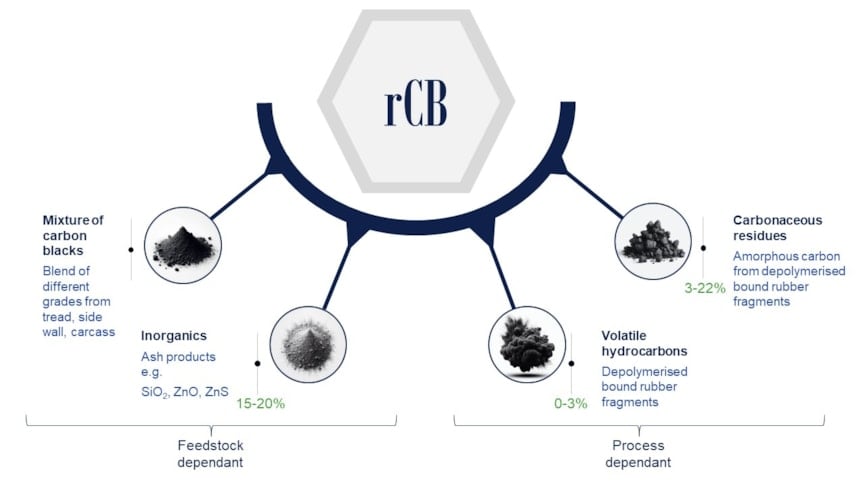
Inconsistency in quality due to variation in ELT feedstock is the main challenge faced during the production of rCB. Standardized product specification is a key need of customers and offtakers, requiring rCB producers to have robust tracking and tracing capabilities, in conjunction with stringent process control measures. Interest in rCB is driven by its improved sustainability and circularity credentials, driven by policy, with estimates of up to 80% reduction in equivalent emissions relative to vCB. Across three impact categories in a life cycle assessment, pyrolysis of ELTs has been shown to be superior to energy recovery via incineration.3
Tyre pyrolysis oils (TPOs)
Cooling the drawn off gas of the original pyrolysis process produces the TPOs, with the remaining gases (e.g. CH4) returning to be combusted for electricity production, treatment, or collection, to minimize environmental impacts. TPOs, also known as thermolysis oils, can act as a feedstock to the mature oil commodity market, with global demand, but high volatility. TPOs can be used as a waste-derived crude substitute for new rubber products, adhesives and coatings or refined into synthetic fuels and renewable diesels.
TPOs benefit from high aromaticity and low sulfur contents, but demand highly depends on the product quality. However, any product that does not meet required specifications can be sold as bunker fuel for ships. The price and category of bunker fuel will be driven by the sulphur content, which continues to be lowered by legislation for use outside of designated emission control areas (IMO 2020). Several large global chemical companies have set circular economy targets for increasing usage of recycled materials.
Diverse market and regulatory landscape: Capitalizing on opportunities in the absence of a one-size-fits-all business model
The tyre manufacturing sector is the biggest consumer of virgin carbon blacks and is therefore the key target off-taker for the rCB product. Manufacturers are looking to increase their consumption of rCB in line with increasingly stringent decarbonization requirements, circularity, and sustainable material goals. Consistent quality and availability are the key driving factors for widespread adoption. Unique regional regulation, systems and collection mechanisms add complexity to the scale up of processing ELTs, as there is no one-size-fits-all business model. Furthermore, restrictions on the export of ELTs outside of the EU, due to the Waste Shipment Regulation,4 encourages local solutions. Variations in tyre composition and quality result in not all types of tyres being suitable for standard processing. However, there remains an opportunity to maximize the value of the waste product and innovation in this industry, driven by policy and the commitments to resource circularity, such as those defined by the European Commission.
The EU Circular Economy Action Plan2 (CEAP) aims to drive the uptake of sustainable products, reduce waste, and make the EU the spearhead of global efforts to establish a circular economy. Key 2030 targets under the Circular Economy Package include:
- Municipal waste: 65% recycled
- Packaging waste: 75% recycled
- Landfilling: Only 10% of municipal waste is landfilled
New legislation is providing incentives, both financial and social, for increased reprocessing of ELTs. This is primarily driven by developed economies, typically in the EU. For example, France’s Anti-Waste Law (2020) seeks to improve the circular economy in the country by reducing waste through actions such as increasing product transparency and reducing the volumes of unsold products that are landfilled5. In July 2020, the UK issued its own Circular Economy Package based on the EU version6 that aligns with the UK’s 25-year environment plan to achieve zero avoidable waste by 2050, an ambition that can only be completed with ELT recycling. In addition to legislative efforts to increase the reprocessing of ELTs, there are voluntary mechanisms under development. In Ireland, REPAK, an environmental not-for-profit organization, is driving financial and tax incentives to promote recycling and discourage downcycling.
Addressing challenges: Reliable end-of-life tyre supply and product demand
Tyre manufacturers have been seen to purchase stakes in rCB producers, with the aim of securing consistent quality and availability of product. However, DNV acknowledges a tangible opportunity for smaller producers due to varying regional regulation defining collection mechanisms and localized availability of feedstock. Securing a consistent and well-categorized source of ELTs will simplify the process and minimize risks. Regions have begun introducing certification programs and standards for sustainable tyre recycling processes to ensure environmentally responsible practices, with significant benefits endowed upon a plant classified as a waste facility. The leading strategy to provide the scale of product required to secure large offtake agreements looks to be cooperation with other rCB producers. Predetermined specifications would catalyse such collaboration between rCB producers, as this is noted to be the largest risk expressed by rCB customers. Other concerns include the lag period between offtake agreement and substantial volumes once operations begin.
![Artist rendition of prescient tyre recycling operations [Dall-E 3]](/contentassets/72bbbea5d28e49f5aa074d8d810b9eee/image83tx.png?mode=crop&width=864)
The offtake of TPO products has fewer challenges, with a strong drive for sustainable feedstocks for production of waste-derived fuels. More stringent sulphur regulation indicates a move to low sulphur fuel oils, notably in Europe, which could lead to higher costs of securing feedstock for vCB. This will, in turn, support rCB prices over time and demand for TPOs.
DNV is cognisant of the difficulty in securing capital for constructing and operating ELT recycling plants in the current market, with short-term Engineering, Procurement and Construction (EPC) tenders and a challenging borrowing climate. However, disruptions to Russian supply, which has historically addressed up to 30% of the European tyre manufacturer demand7, have led to manufacturers looking for a more consistent, domestic supply. The volatility in the vCB market and high crude oil prices support rCB prices in the near term, replaced by sustainability requirements and 80-90% reduction in carbon footprint in the longer term. Respected LCAs will be necessary to prove sustainability claims and confirm true circular operations.
As global vehicle ownership grows, the number of discarded end-of-life tyres (ELTs) is expected to rise, amplified by the transition from petroleum-based vehicles to electric ones. DNV expects manufacturers to face rising cross-sector resource circularity pressures from legislation and societal incentives but maintains that these very policies are crucial to address the transition challenges and move towards circularity in waste management. Significant progress has been made in processing ELTs, yielding recycled steel, recovered carbon black (rCB) and tyre pyrolysis oils (TPO). Despite complexities, DNV expects growth in demand for rCB and thermolysis oils over the coming decade, as they offer a more sustainable alternative to the virgin product equivalents in terms of carbon footprint and resource efficiency. DNV expects rCB and TPO products to gain prominence particularly in Europe, where the EU Green Deal and the EU Circular Economy Action Plan will enact tighter targets under key relevant waste/recycling directives over the coming decade.
4/11/2024 7:25:00 AM