Safe implementation of decarbonization technologies
Integrating new technologies on board vessels involves understanding safety risks and implementing mitigation measures. DNV’s class notations and guidelines facilitate this process, ensuring a safe transition to a zero-carbon future.
Safety considerations should be part of every decision to adopt a particular technology or modify a vessel. While some technical efficiency enhancements, such as propeller retrofits, passive air lubrication or hull modifications, typically do not influence the on-board routines, others, including wind-assisted propulsion systems (WAPS), shore power, battery systems, active air lubrication systems and alternative fuels, introduce risks related to structural integrity and new procedures on board or changes to existing ones, which need to be accounted for.
Furthermore, most technical modifications require class approval. DNV class notations exist for many enhancements and are mandatory if relevant measures are implemented. For major retrofitting projects, a comprehensive risk assessment is generally advisable and, in many cases, required by class or the authorities, especially where the regulatory environment is incomplete.
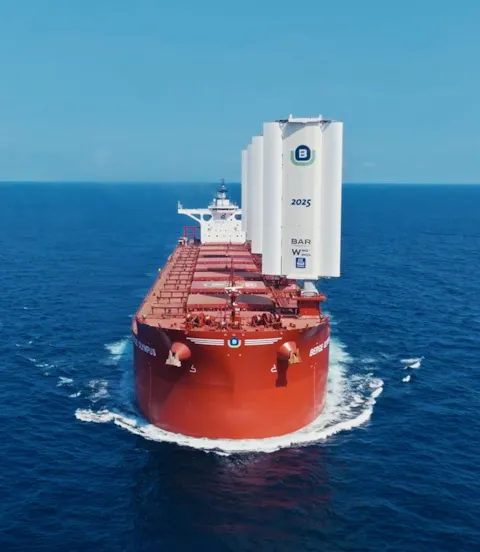
Safe and efficient integration of wind-assisted propulsion
WAPS change the loads acting on the vessel structure as well as the ship’s aerodynamics and manoeuvrability significantly. Furthermore, they have an impact on port operations and may interfere with overhead structures such as bridges when operating in coastal areas. Ensuring the ship’s structural fitness for WAPS and the chosen system’s robustness, reliability and operational safety in harsh marine environments is critical, requiring thorough testing.
WAPS can interfere with the line of sight and the visibility of navigation lights, and affect the radar blind sector, all of which have implications for compliance with statutory requirements. In some cases, WAPS may induce noise and vibration which can affect crew comfort and vessel integrity.
Navigating a ship with active WAPS takes experience and skill and typically requires updates to on-board practices, safety protocols, maintenance routines and equipment. Control systems for the propulsion engine and WAPS should be integrated to allow the efficient coordination of both. Comprehensive crew training is essential to ensure safe and efficient WAPS and vessel operation.
DNV rules ST-0511 define structural design loads and associated safety concepts for WAPS for designers and manufacturers. The class notation WAPS is mandatory when installing WAPS on an ocean-going vessel. DNV offers its Approval in Principle (AIP), Type Approval Design Certificate (TADC) and Type Approval Certificate (TAC) as WAPS technology qualifications.
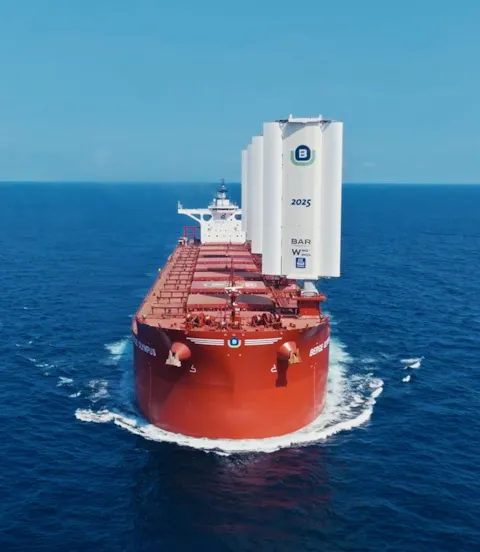
Safety essentials for active air lubrication systems
Active air lubrication systems (ALS) on ships must meet stringent safety requirements to ensure safe and effective operation. These include approval by a classification society, structural assessments to account for hull modifications, and integration with ship stability calculations. Machinery components such as air compressors and piping must be marine-grade and equipped with overpressure protection. Continuous monitoring, automatic shutdown features and integration with the ship’s automation systems are essential for optimal performance. DNV has issued a recommended practice for establishing a standard for verification of the performance of air lubrication systems.
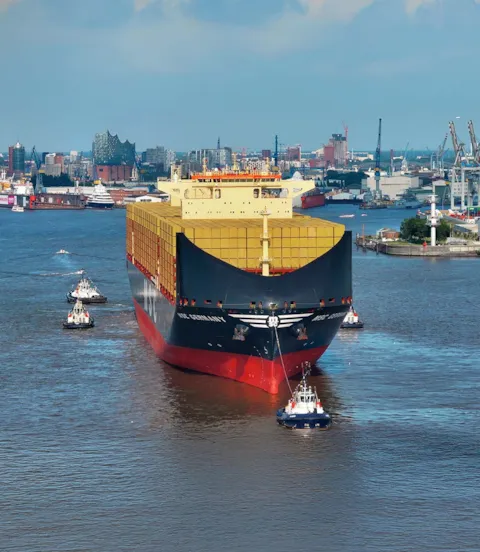
Improving hull cleaning safety with ROVs
As one of the most straightforward efficiency enhancements, hull and propeller cleaning can either be performed during dry docking or during cargo operations in port, where permitted. Conventional hull cleaning by divers involves several safety risks. Remotely operated underwater vehicles (ROVs) equipped with high-pressure water or cavitation systems or hull cleaning through the automatic collection of waste products, using specialized equipment to remove biofouling from the hull while simultaneously capturing debris, offer a non-destructive alternative to divers, eliminating the associated safety risks. However, ROVs cannot access certain areas of a ship hull, such as thruster tunnels, so some diver-assisted operations are still necessary. Some regions have mandated clean hulls and proper debris management based on the IMO Biofouling Guidelines, making compliance essential to prevent the spread of invasive species and protect marine ecosystems.
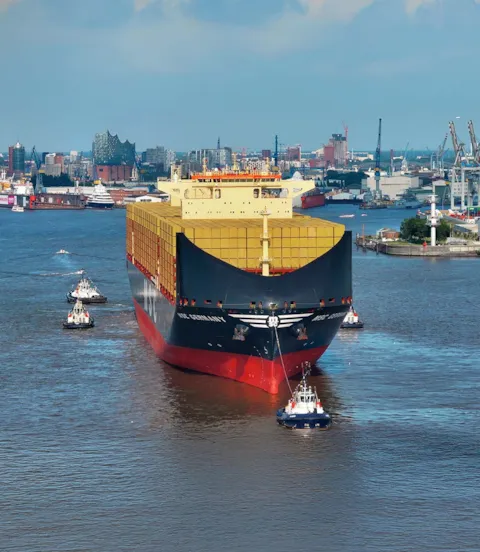
Wind shields: Ensuring visibility and stability
Installed for aerodynamic optimization, wind shields may have an impact on safety by compromising the line of sight from the bridge, or affecting ship stability. Modifications should follow DNV-RU-SHIP Pt.5 Ch.11. Class approval is required if modifications alter the structural integrity or primary safety features. Clear visibility must be maintained at all times, and defogging or heating systems should be functional in cold climates to prevent icing or fogging.
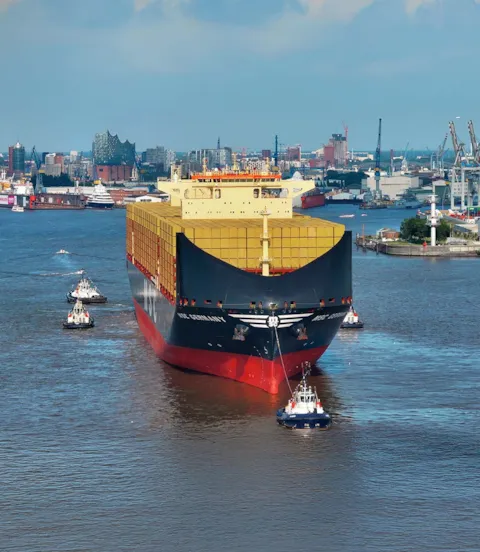
Mitigating lithium-ion battery risks
Lithium-ion batteries introduce the risk of thermal runaway, which increases the fire, explosion and toxicity risk on board the vessel. Safety measures such as thermal runaway propagation protection, sufficient ventilation and fire suppression need to be implemented. The DNV class notation Battery(Safety) is mandatory for the installation of (li-ion) batteries larger than 20 kWh, while Battery(Power) is required if the vessel depends on batteries for propulsion. Additionally, some flag states have guidance for battery installations that might be applicable.
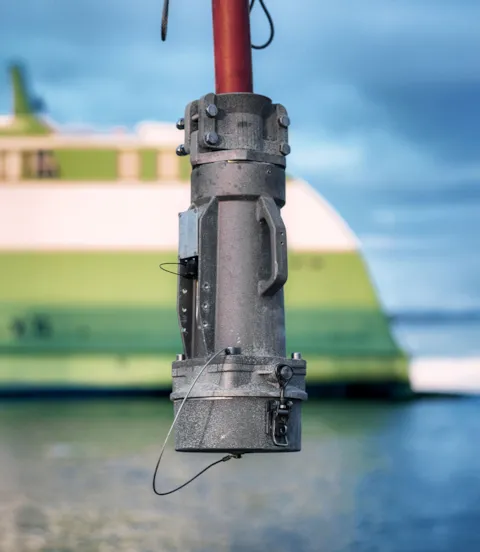
Ensuring safe shore power connections
Under FuelEU Maritime, shore power will become mandatory from 1 January 2030 for containerships and passenger ships above 5,000 gross tonnage calling at EU ports. Connecting and disconnecting shore power cables can expose operators to electrocution risks and pose an explosion risk if flammable vapours are present. To mitigate these safety risks, operators should ensure that the electrical connection is not live (for example, it has to be isolated and grounded) and wear appropriate personal protective equipment. Ideally, shore power connections should be placed away from areas with flammable vapours. If this isn’t possible, ensure the environment is safe during both connection and operation. Additionally, implementing automatic disconnect systems and conducting regular safety training can further enhance safety. Interim guidelines issued by IMO provide guidance and recommendations to enhance safety. The DNV Shore Power class notation includes a set of general requirements for shore power designed to be flexible. IMO has issued MSC.1/Circ.1675, Interim Guidelines on Safe Operation of Onshore Power Supply (OPS) Service in Port for Ships Engaged on International Voyages. Port-specific safety requirements may apply in addition.
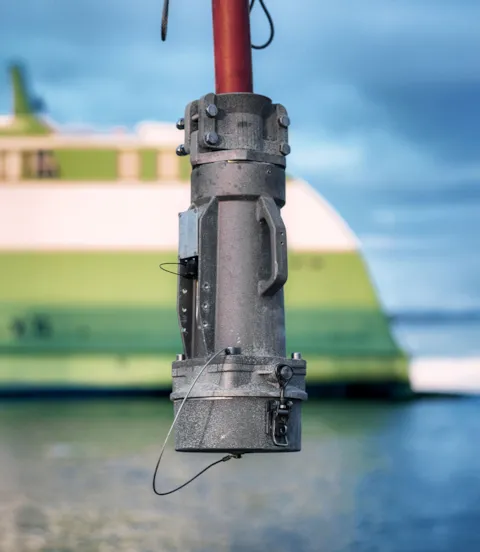
Improving safety of dynamic positioning (DP) systems
The operation of DP systems is highly energy-intensive. Power system upgrades using closed bus-ties optimize energy usage and minimize carbon emissions from gensets through optimal battery use for peak shaving and load balancing. However, industry adoption of closed bus-ties has been hindered by concerns over failure propagation. To address this, DNV has revised its recommended practice (RP) RP-0591 for redundant dynamic positioning systems with closed bus-ties. New fuel-efficient designs must ensure sufficient safety for all planned DP operations by updating safety barriers, incorporating additional protection and monitoring facilities, and validating fault tolerance through rigorous testing.
Magnus Jordahl
Senior Consultant
- Berge Bulk
- Alfa Laval
- Hasenpusch Photo-Productions
- Shutterstock / JodGy
- Shutterstock / Jegor Glushenkov