The future of remotely operated machinery
Remote operation of onboard machinery offers an attractive array of advantages for shipowners and operators. DNV GL is working with Høglund, Fjord1, and the Norwegian Maritime Authority in a research project to explore the idea of moving the engine control room from the ship to a shore-based centre, while ensuring a safety level that is the same or better than today’s conventional operation.
As ships become more complex, shipowners have found themselves increasingly reliant on suppliers to operate and maintain their vessels. Some are also struggling to recruit from the new generation of machinery engineers. “Electronics and data systems on board require steadily higher levels of competency, but young engineering talent tends to prefer shore-based jobs,” says Steinar Låg, Principal Researcher on Autonomous Ships at DNV GL.
Control doesn’t have to mean close
In response to this rising challenge, DNV GL joined forces with the automation systems vendor Høglund, the Norwegian ferry operator Fjord1, and the Norwegian Maritime Authority to establish the ROMAS project. ROMAS stands for remote operation of machinery and automation systems and focuses on moving the engine control room (ECR) from the ship to a shore-based engine control centre (ECC). There, a team of one or more chief engineers can remotely operate the propulsion and auxiliary machinery systems on a whole fleet of vessels. “Our focus is on identifying the required technical solutions and establishing a regulatory framework with rules and verification methods for remote shore-based operation of ship machinery and automation systems,” explains Låg, who manages the ROMAS project.
“Transferring responsibilities, monitoring and control facilities to shore reduces the need for machinery engineers on board and should make marine engineering jobs more attractive,” he adds. “Automation and remote operations are increasingly being adopted in other industries, and shipping is taking the first steps toward autonomous sailing. Engine room automation has been around for a long time, so this concept builds on existing technologies and is an essential step toward a fully autonomous or highly automated vessel.”
Kim Gunnar Jensen, project engineer at Fjord1, notes that the company is investing heavily in electric and hybrid ferries. “These vessels will support a safe and efficient transport system, but the digital and connected solutions on board also enable more remote operations with increased shore support for improved safety and efficiency. ROMAS is a research project that provides us with an arena to explore these possibilities and find solutions for a new generation of ferry transport that will benefit all stakeholders.”
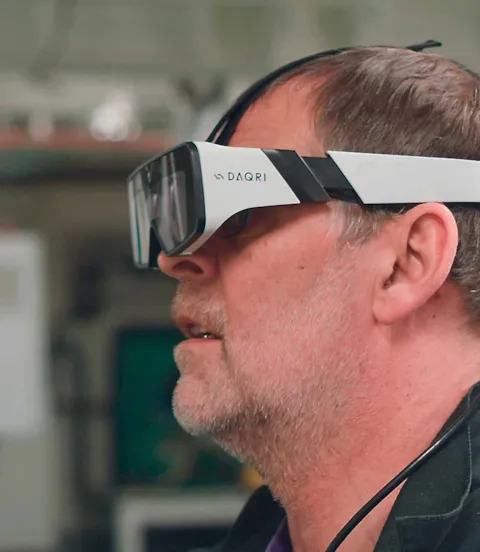
New knowledge enables new ways of working
New approaches to design and operations, combined with increased redundancy and more advanced maintenance, mean that the concept could conceivably be operated with no machinery engineers onboard at all. “Once this step is taken, the way to more autonomous ships becomes clearer and shorter,” says Låg.
The project commenced in 2017 and will continue to the end of 2019, supported by funding from the Norwegian Research Council. In the pilot test campaign, Høglund Marine Automation is responsible for equipment on board and at the engine control centre on shore. Machinery monitoring and control will be centred around Høglund’s existing integrated automation system (IAS), but the implemented solutions will also include alarm improvements, closed-circuit television surveillance and a reliable and redundant communication solution based on 4G modems.
The project manager for this project in Høglund Marine Automation, Didrik Høglund, comments: “This project has verified the basic system functionality and is setting a standard for the future control systems for remote operation of vessels.”
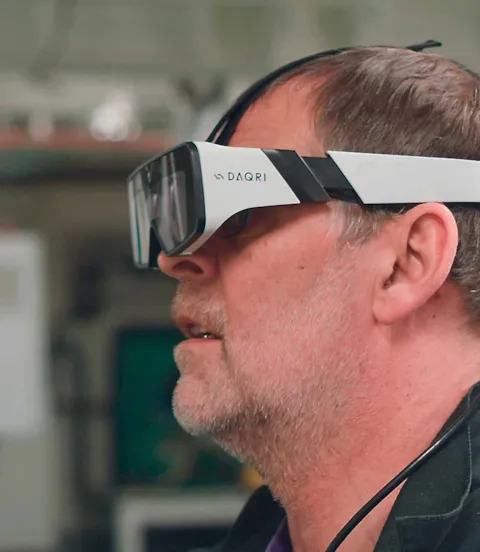
Testing the way to safe operations
Activities carried out in the project in 2017 and 2018 included identifying business and user requirements, mapping relevant rules, regulations and risk considerations, and performing data analysis. This work followed the process outlined in DNV GL’s class guideline for autonomous and remotely operated ships (DNVGL-CG-0264) and included development of a concept of operations (CONOPS) document and conducting a hazard identification analysis (HazID), that provided the basis for the pilot test campaign.
For the test campaign, the ECC was established at Fjord1’s office in Molde. The aim of the testing is to gather data and experience that can be used to validate assumptions and give input to rule development in order to ensure safe commercial deployment of the concept in the future.
The campaign was carried out with one of Fjord1’s ferries, the Fannefjord. Built to DNV GL class in 2010, the vessel is a modern and highly redundant LNG/battery/diesel-powered ro-ro ferry operating on the 35-minute crossing between Molde and Vestnes. While the ROMAS concept may be applied to longer-range voyages in the future, shorter crossings employing modern vessels offer a more suitable operational profile for testing and verification of the concept.
Various test scenarios have been introduced during the first pilot period, including functionality and procedures related to loss of communication. Smart glasses using augmented reality (AR) were also tested for remote troubleshooting. Remaining work in the project will focus on documenting pilot experiences, rule development and dissemination activities.
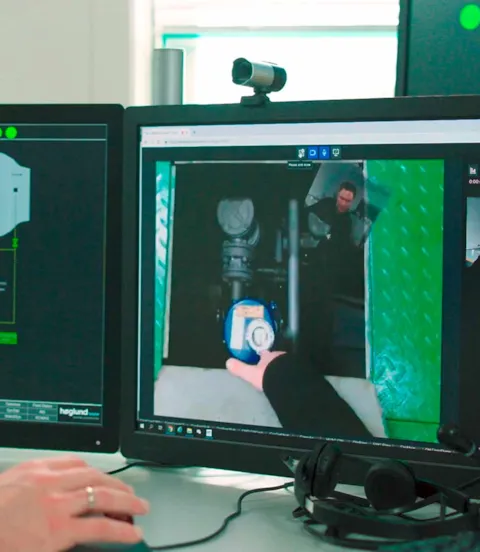
Remote means new crew solutions
Manning at the ECC will be round the clock with one operator in the role of chief engineer and arrangements for additional support. The ECC is designed to support three ferries with similar design and operational profiles, but only one ferry will be operated in the pilot phase.
In the ro-ro ferry segment, safety manning normally determines the overall manning level. In order to comply with this requirement, overall manning on the ferry will remain unchanged at five crew members. The chief engineer on board will be replaced by a multiskilled seafarer with the ability to take command of technical systems as needed. The ECR and bridge workstations will function as backup for the ECC. In other ship segments like cargo, with lower safety manning and a higher ratio of machinery engineers, the concept could potentially enable a reduction of the overall number of on-board crew.
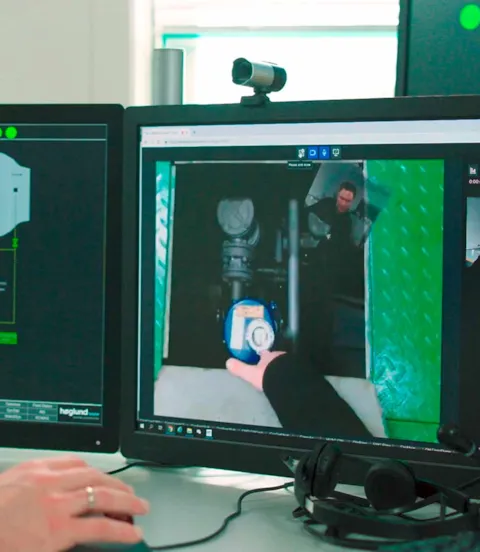
Building for a remote future
A remote IAS will serve as the hub for monitoring and controlling the machinery and engineering systems. IAS functional enhancements will also be implemented, such as communication system integration and functionality for synchronizing data and transfer commands between ship and shore.
The IAS network on board is connected with the ECC by a reliable and redundant ship-to-shore communication link. Portable communication devices and AR equipment are used not only for troubleshooting, but also to ensure efficient support of the crew from the ECC. A wide range of normal and abnormal operations, conditions and scenarios have been mapped and a division of responsibility between the ECC and on-board crew established.
“The long-term plan is to use project learning for future operations and development of new products and services,” says Steinar Låg. These include a “Remote Ready” IAS system from Høglund, applicable rules and Approval in Principle programs from DNV GL, and regulations from the Norwegian Maritime Authority. “The aim is to enable Fjord1 and other ship owners to consider commercial deployment for new generations of ships,” he concludes.
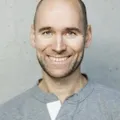
Steinar Låg
Principal Researcher
- Løken - CC BY-SA 3.0 (https://creativecommons.org/licenses/by-sa/3.0)
- Fjord1