Pushing the limits
The award-winning yacht Pink Gin, launched in June 2017, is the world’s largest all-carbon-fibre sloop. The designers and engineers worked closely with the classification society DNV GL to make her owner’s visions a reality.
A luxury sailing yacht is not only expected to have excellent sailing performance but also to offer all the comfort and amenities that the word ”luxury” implies. In fact, features that had been reserved for larger and more robust motor yachts are increasingly finding their way into pleasure sailing – where they are much more difficult to engineer into the overall concept because of the stringent structural and weight restrictions imposed by sail propulsion.
Pink Gin is not an unknown name in the superyacht world. When owner Hans Georg Näder decided to order the next generation Pink Gin VI, he was envisioning a number of enhancements over her predecessor, Pink Gin V: a record hull length of 53.90 metres, a 67.90-metre mast, accommodation for a total of 20 persons and, most notably, two fold-out balcony doors, a standard feature on motor yachts but never before seen on a carbon sailing yacht.
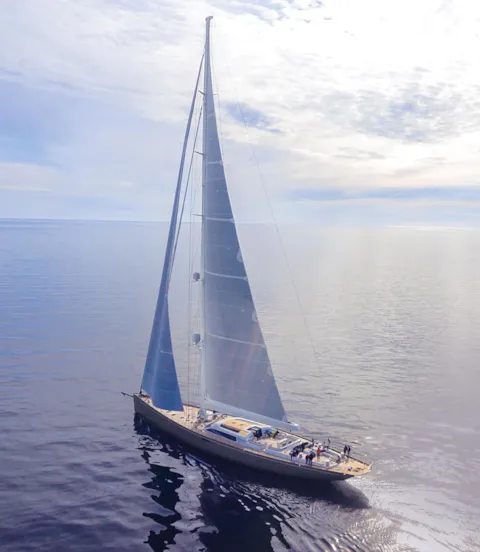
Interdisciplinary collaboration
A carbon-fibre hull is a complex, highly sophisticated structure that must be able to handle the loads and torsional forces from wind and waves as a single, coherent organism. Cutting two sizable holes for balcony doors into such a hull seems daring. But Näder, a passionate sailor, knew that his proven partners, naval architects Judel/Vrolijk & Co. of Bremerhaven, the British stylists Design Unlimited, and Baltic Yachts in Finland, would find a way to make it happen; after all, they had worked together successfully for many years. The structural engineering work for the carbon-fibre hull was placed into the trusted hands of Gurit Composite Engineering in the UK, and DNV GL was chosen as the classification society.
So the designers and engineers went to work. An analytical approach and a design concept were agreed with DNV GL at an early stage to define core parameters for the subsequent development work. This cooperation continued throughout the project to make sure the finished boat would fulfil all class and flag state requirements.
Finite element analysis (FEA) models of the entire ship, the rig and several other crucial details were generated to simulate and study all design alternatives thoroughly and identify weight-saving potential before deciding which way to go.
In spite of all the extras, it is still a lightweight hull: “A 250-tonne displacement is relatively low for a yacht of this type and size. It was achieved by using advanced carbon sandwich hull and deck construction methods,” explains Hasso Hoffmeister, Senior Principal Engineer at DNV GL. Even the construction sequence was painstakingly coordinated with the yard: “For example, the hull topsides were produced separately and joined to the hull bottom after most of the interior structures had been fitted.”
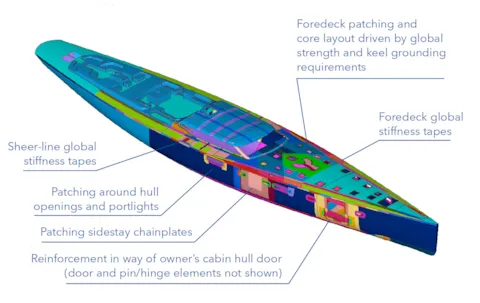
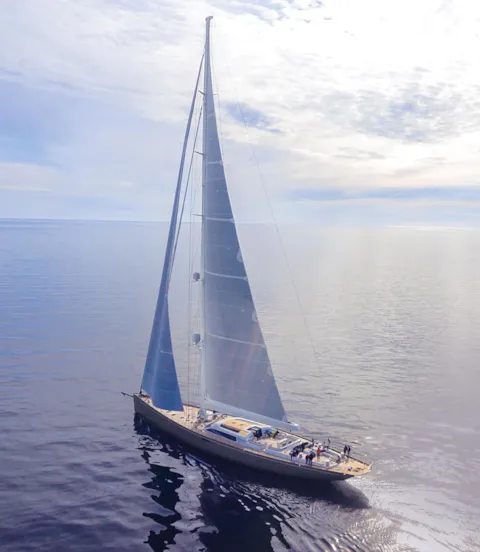
A combined solution
Integrating the balcony doors into the overall structure of the yacht without sacrificing global strength was the toughest challenge. The balcony of the owner’s suite is located in the fore ship, between the mast and the forestay. Considering the maximum compressive force of 300 tonnes from the 67-metre mast, and a maximum tension of 60 tonnes on the forestay, the forward hull section must withstand enormous forces while sailing. The second balcony door was to be located in the lobby area on the opposite side of the ship. The designers had to make sure that neither the doors nor their opening mechanisms would warp, and that the global strength and overall integrity of the ship would not be affected by the openings,
which extend over 75 per cent of the local freeboard. In other words, the balcony doors had to be made integral parts of the ship’s structure. This was accomplished by combining hydraulically actuated hinges at the bottom corners of each door with transverse retractable locking pins in the upper corners. When the doors are closed, these four elements firmly interlink the doors with the hull, making sure all forces are distributed evenly. Two additional pins keep the closed doors tightly sealed against sea water. “The verification of carbon composite hull structures is always a complex task,” says DNV GL’s Hasso Hoffmeister. “What was extraordinary on this yacht was to identify and secure loading scenarios for the integrated doors. There were no sources of knowledge available and this hasn’t been defined in our class rules so far. The design and review loop included probabilistic methods and it was pioneering work for all parties involved.”
Another challenge for the design engineers was the lifting keel. Weighing in at 71 tonnes and adjustable in three vertical positions, the keel gives the ship a flexible draft ranging between 4.5 and seven metres. The design and integration of the keel lifting appliances into the hull was a joint effort between the keel manufacturer APM, Gurit and Baltic Yachts. Fine element (FE) modelling was used to study the interplay of forces and determine the best way of building up the laminate. High precision in the fabrication process was essential to prevent imbalance or uneven bending behaviour of the structure under load.
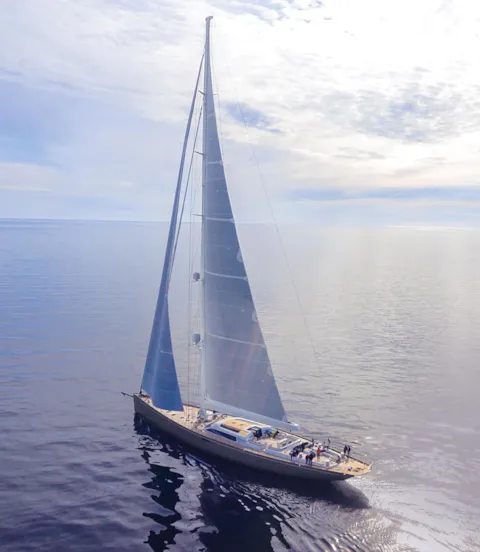
State-of-the-art rig design
An important aspect of DNV GL’s role in the project was to certify the rig. Based on its own criteria for the assessment and approval of large modern yacht rigs, DNV GL offers rig analysis, rig certification and rig design certification as well as MCA LY3 compliance certification services. “All yachts larger than 30 metres are prototypes,” explains Johannes Werner, Senior Engineer Structure, Special & Light Craft, IWV & EC at DNV GL. “Their rigs are always unique and state of the art.” Certification began by reviewing the rig design data and assessing the materials, dimensions and load data. An FE model was built and analysed under a variety of sailing load cases. The practical portion of the certification procedure comprised a visual assessment of the physical mast and rig components and monitoring of the mast stepping process.
This was followed by a series of sea trials, including specific manoeuvres and scenarios while capturing the related load data using sensors on board. The results were compared with the calculated data to identify any discrepancies. A final visual inspection of the mast and the upper parts of the rig concluded the service. All results were documented, whereupon DNV GL issued the Rig Design Certificate, and the MCA LY3 Compliance Statement (Large Yacht Code of the British Maritime and Coastguard Agency).
Since her launch from the shipyard in Jacobstad, Finland, Pink Gin has won the Sailing Yacht of the Year title and the Sailing Yachts 50 m and above category at the World Superyacht Awards 2018. She has visited South America, the Caribbean, the Mediterranean and the Baltic, and seeing this unusual, innovative craft plough the world’s oceans is not only an aesthetic pleasure but also a source of immense joy and satisfaction for the designers, engineers, experts and craftspeople who have jointly accomplished all this.
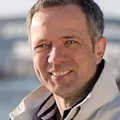
Hasso Hoffmeister
Senior Principal Engineer