How to sculpture an asymmetric stern
Advanced computer technology and modelling techniques are helping revive an old idea: twisting the stern section of the hull to optimize flow and save fuel.
The history of shipbuilding harbours many surprises, and the biography of Ernst A. Nönnecke is one example: a trained shipbuilding engineer and an accomplished opera singer at the same time, Nönnecke, born in Hamburg in 1921, had a reputation for his intuitive, rather artistic approach to shipbuilding; was also a sculptor. In the late 1960s he came up with the brilliant idea of designing a ship with an asymmetric stern to account for the different flow conditions to the right versus left side of the propeller. His concept for optimizing flow and propulsion efficiency came more than a generation too early, however: the manual calculations proved to be extremely tedious, and implementing the design at the yard was even more tricky – and costly.
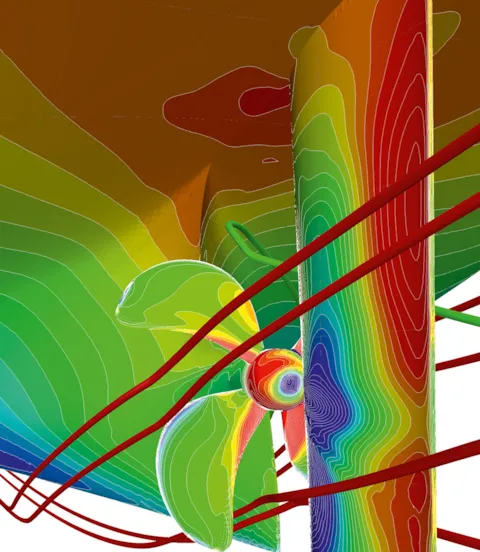
IT brings the breakthrough
But Nönnecke’s invention was by no means a wasted effort. It was implemented various times during the following decades, if with great effort, and the few ships built with twisted aft sections did prove the merits of the concept as an elegant alternative to retrofitting so-called pre-swirl devices such as fins or ducts to optimize the utilization of the propulsion systems‘ rotational losses.
But the real breakthrough came more recently, enabled by high-performing computers and advanced software. “What computers can do so much better than people,” explains Dr Karsten Hochkirch, Head of Department – Fluid Engineering at DNV GL, “is find the right balance between improved propulsion efficiency and increased resistance.” This can be accomplished only by performing complex iterative calculations for a large number of design variants – a perfect job for computers.
High-fidelity computational fluid dynamics (CFD) today provides the right toolset for designing complex shapes efficiently. Used in combination with the formal parametric optimization procedure developed by DNV GL, this approach makes design optimization much more manageable and efficient. Within the scope of its ECO Lines hull design optimization services, DNV GL now offers asymmetric stern optimization. The procedure gives significant freedom in shape variation without altering the key design requirements. Using special CFD tools and custom-developed code tested and proven in hundreds of towing tank trials, the DNV GL experts combine ship and propulsion simulation techniques based on viscous Reynolds-averaged Navier–Stokes (RANS) equations with dedicated, state-of-the-art propeller analysis code to determine the propulsion efficiency of a given model with high accuracy.
The formal hull shape optimization procedure begins by defining the objectives and optimizing the parametric model of the ship. What follows is a cyclic, iterative process to select the best-performing solution out of thousands of virtual model variations. In the RANS cycle, which is part of the routine, the results of the viscous flow calculations are used as input to the propeller computation tool, whose output is then fed back into the next round of viscous flow calculations. In a final stage, the most efficient models undergo virtual towing tank tests until the best variant has been identified. This entire process requires enormous computing power: “There are around 7,000 CPUs in the basement of the DNV GL building doing the work Nönnecke did by himself,” Hochkirch points out. When all computer work is done, a real-life scale model of the final design is built and taken to a traditional towing tank to verify the data.
The actual production processes at the yard have become much simpler as well thanks to advanced CAD/CAM techniques and modern, CNC-controlled fabrication methods.
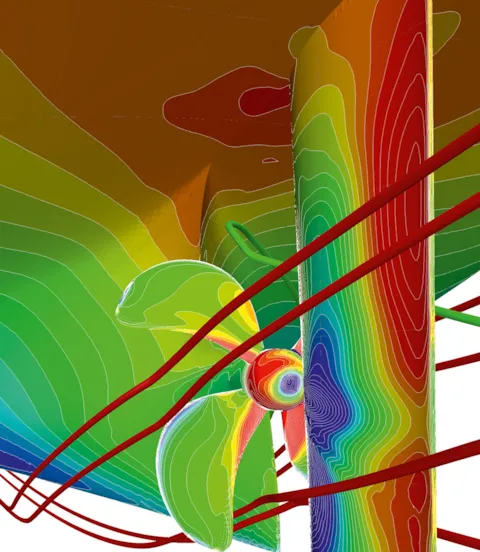
Considerable fuel savings
Several projects have demonstrated the potential of the DNV GL approach. In the case of a handymax bulk carrier design, the resulting twisted stern enabled a four per cent decrease in propulsion power compared to the original design. In another project, a 3,000 TEU container ship was to be modified to minimize power consumption. Starting from a well-optimized symmetric baseline design, the asymmetric aft ship reduced propulsion power by three per cent, a result confirmed in model tests.
These and other examples have shown that the achievable gains in propulsion efficiency are generally higher for bulk carriers and tankers than for container ships. Depending on vessel design and operating profile, fuel efficiency improvements of up to five per cent are possible when starting from a well-designed symmetric baseline. Added benefits of a twisted stern include higher structural robustness and minimized vibration and fatigue.
The Fluid Engineering team at DNV GL can draw on decades of experience pioneering parametric hull line optimization. Implemented in close cooperation with both the customer and the yard, its ECO Lines asymmetric stern optimization service ensures reliable calculations, confirmed results from proven experts, and accurate execution at the yard. Ernst A. Nönnecke’s ingenious idea is finally coming to full fruition.
Dr Karsten Hochkirch
Head of DNV’s Ship Performance Center