The heavy-lift fleet of the future
Success in the fiercely competitive global MPV market hinges upon flexibility, efficiency, reliability and the ability to handle whatever cargo the market offers. A new design is leading the way.
“Something is bound to happen there,” says Frank Fischer, Managing Director of Tonnage and Procurement at Intermarine, a ship operator based in Houston, Texas. Ship operators and charterers are still holding back on ordering new ships. But the MPV fleet in the market is now relatively old while the trend towards more valuable and larger-sized cargo continues. Flexibility, efficiency and reliability are key, and new environmental regulations are driving up the cost pressures. “Older tonnage is going to disappear from the market in the medium term,” Fischer assures.
But Intermarine did not want to wait that long and the company is steadily modernizing its fleet to keep up with future standards while providing a stable capacity to its clients. The first in a series of eight new F-Class 900 vessels will be delivered in spring 2018. Classed DNV GL, the 13,300 dwt Ecolift F900 vessels will be equipped with two cranes with a 900-tonne combined lifting capacity. DNV GL provided pre-project support, annotating the specification documents and draft designs to ensure operational flexibility and flawless interaction of the entire on-board ecosystem of cranes, holds, hatch covers, tween decks and sea fastening equipment.
The newbuilds will operate under a long-term bareboat with China’s CSSC Leasing. Hamburg-based Hammonia Reederei is overseeing the construction process and will provide technical ship management services. The vessels are being built at CSSC‘s shipyards in Hudong and Huangpu Wenchong.
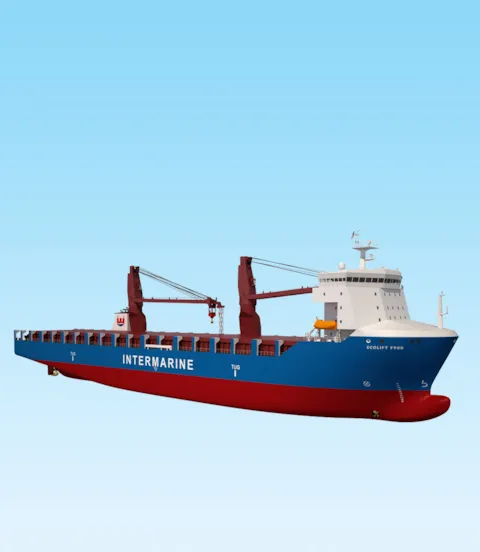
Versatility and good utilization
Since 2011, Intermarine and Hammonia have been gaining operational experience with a wide range of heavy-lift/MPV vessels since 2011. The new Ecolift F900 is the logical and innovative followup to this ship type. It is designed for maximum efficiency and cargo flexibility – whether handling break-bulk, dry bulk, project or heavy-lift cargo. Notably, the Heavy-Lift Box-Hold MPV Tweendecker (as this vessel type is officially called) measures 150 metres in length and 25.6 metres in breadth with an 8.3-metre draught and can transport a broad variety of cargo anywhere in the world. This includes less-travelled routes, remote areas and small ports without advanced infrastructure.
The most likely scenario for future deployment of these ships is a well-filled cargo hold without utilizing their full cargo capacity every time. Hammonia, the developers of the new F-Class focused on maximizing cargo space and ensuring cargo flexibility. “One of our key objectives was the ability to load and unload cargo without using stabilization pontoons,” says Captain Rochus Schneider, Fleet Manager at Hammonia. “Pontoons occupy valuable cargo space on board, and handling them takes precious time.” Speedy port operations are a key concern for all parties involved.
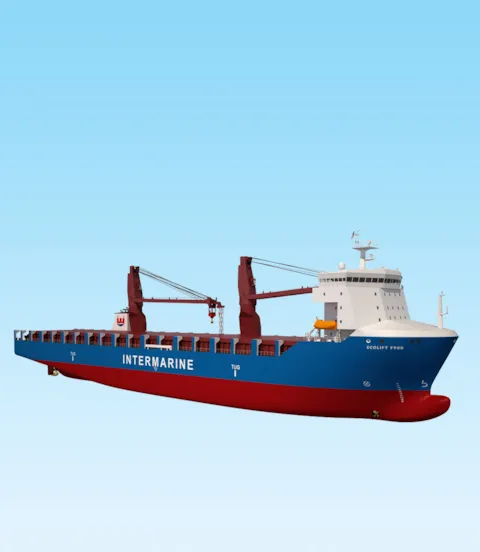
Maximizing cargo flexibility
Break-bulk and project cargo, such as power stations, wind turbines and reactors, is typically shipped in modules or sized as big as the available means of transport will allow, which often requires the cargo hold to remain open. “The Hatchcoverless class notation was a must for these new ships,” says Schneider. The tank top can bear deck loads of up to 25 tonnes per square metre, and the cargo holds and access openings offer the greatest possible flexibility. “We can combine the tween deck levels in hatches as needed,” says Fischer. The weather deck hatches are aligned with the tween deck hatches so the slots are directly accessible down to the tank top at any time. “This is important for stowing containers – it allows us to unload part cargo as needed,” says Fischer.
Of course, every cargo hold has its limits. While an Ecolift is able to carry items such as wind turbine rotor blades up to 105 metres in length on tween decks, longer ones have to be placed on the weather deck, possibly extending beyond the ship’s stern. To avoid additional class or flag state conditions being imposed upon the F900 fleet for open-hatch operation or overlength cargo, Intermarine, CSSC and Hammonia agreed to place the deckhouse near the bow. “Doing so avoids blind sectors when carrying tall cargo that would require an additional fore mast radar unit,” says Schneider. The deckhouse, which features integrated lateral wave bays, doubles as a breakwater. To accelerate cargo loading the project partners opted in favour of a combined hatch cover system by TTS. The forward and aft cargo holds use hydraulic folding covers. The amidships main tandem-lift working area is equipped with reinforced pontoon covers that can support up to eight tonnes. “This means we can place heavy objects such as a 4,000-tonne cable carousel on these covers,” says Fischer. Pontoon-type hatch covers are also low-weight and easy to maintain.
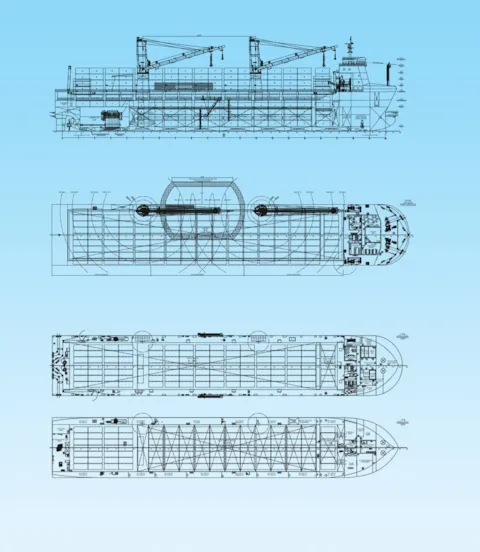
Innovative cranes
The most important equipment on board a heavy-lift cargo vessel is its cargo lifting gear. “For the time being we decided in favour of proven electro-hydraulic cranes,” says Schneider. But that might change as Hammonia is involved in an EU project for the development of all-electric cranes. This would promise a number of benefits including: a more straight-forward design, lower weight, easier maintenance and improved environmental compatibility.
Typical MPV ships have two large cranes and an auxiliary crane. McGregor custom-developed a crane with an extended jib for the new F-Class to maximize the accessible stowage area and enable the more flexible placement of cargo. “This makes the auxiliary gear redundant,” explains Schneider. Capable of lifting up to 450 tonnes each, these cranes have a 17-metre outreach under maximum load and can lift up to 900 tonnes in tandem operation. Both can provide high lifting capacity across the entire deck area. The long jibs also allow oversized pieces of cargo to be loaded. During sea transport the jibs can be topped up to maximize the usable deck area. The two cranes can be operated in master-slave mode by a single operator. A remote control system could be retrofitted at a later time, but for now, crane operation, and especially heavy lifting jobs, will be the job of experienced crews.
Fast, independent loading and unloading is essential, especially in small ports lacking adequate lifting infrastructure. As MPVs carry more and more containerized cargo, speedy loading and unloading is essential. Competition across the segment and beyond is fierce amid overcapacities and low freight rates across the market. “Today every major container ship operator has a specialized heavy-lift department,” Fischer points out.
The volume of traditional MPV cargo in the market is no longer sufficient to keep the fleet busy. Even large car carriers compete for project and heavy-lift cargo. “Trades in our market have changed,” Fischer remarks. Bulk cargo is an important source of income, so a Bulk certificate is very important for the new F-Class ships. As for the traditional MPV segment, coordinating jobs is getting more challenging. Nowadays, major industrial customers tend to put a single general contractor in charge of all transport tasks. Fischer provides an example: “If a customer wants to build a new factory overseas, the chosen carrier may have to handle as much as 350,000 cubic metres of mixed cargo.” Jobs such as these must be planned at least six months in advance. Customers want to know how their cargo will be transported and lifted, and demand appropriate documentation and calculations. The ship operator’s Transport Engineering department provides this information, and subsequently chooses the ship type to use. The actual vessel will be picked at a later time. “You have to have a large fleet of compatible ships to carry out these kinds of orders efficiently,” says Fischer.
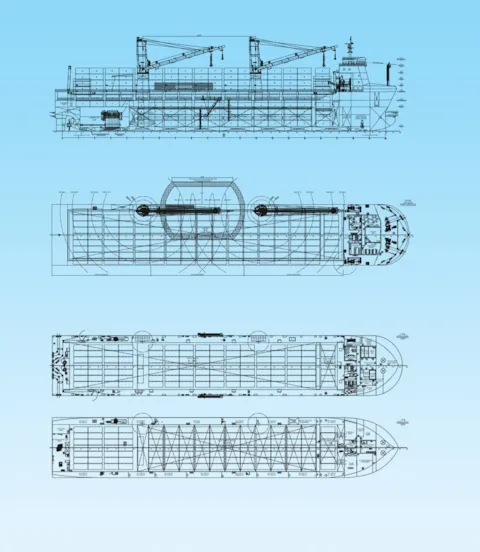
Backed by class
From the start, class has played a key role in innovative newbuilding projects; this is not an exception especially when speaking of the new F-Class. “Close collaboration with the yard and designers is easier when class provides support at an early stage,” says Schneider. The outcome is an entire bundle of optimization measures. For example, the hull of the Ecolift F900 has an entirely new lines plan optimized for the assumed operating profile. The fully balanced twisted leading-edge rudder with a propeller cap customized by Wärtsilä was developed specifically for this vessel type. Trim optimization, stability and stowage software are all part of the standard package. DNV GL created a global finite-element (FE) model of the vessel to analyse the structural integrity of the ship under the high and complex loads acting on the hull with its long cargo hold which helped identify where the ship needed structural reinforcement. This was especially important when the two heavy-lift cranes operate in tandem. The design accounts for the standard load cases specified by the new DNV GL rules to ensure flexibility and transparency.
The same FE model can be later used for supercargo calculations. Customers demand detailed proof that the ship is capable of handling their cargo. “Reusing the FE model lowers costs and delivers highly accurate results quickly over the entire lifetime of the vessel,” says Jan Rüde, Ship Type Expert MPV, Ship Structures and Outfitting at DNV GL.
Optimizing the cargo space was a key criterion when selecting the propulsion system. The two-stroke 7S40 ME-B9.5 was chosen for its efficiency and its lower overall height. Certified by DNV GL, it cranks out 4,800 kW at 105 rpm at 85 per cent of maximum continuous rating (MCR). Three diesel generators provide electricity. Intermarine and Hammonia decided against using battery packs, due to the belief the technology has not reached sufficient maturity.
In autumn 2018, once commissioned, the first ship will immediately begin transmitting performance, monitoring and other operational data to shore. The experience gained with the first of the new F900 class vessels will be crucial for the remainder of the series.
Nothing will be left to chance: the future crews will train at headquarters while the ships are still under construction. There is no question that Intermarine will be a strong competitor in the MPV liner and chartering shipping market. The fleet of the future will soon be ploughing the seas.
Jan Rüde
Ship Type Expert MPV