Ships for the long haul
With the global LNG distribution network rapidly expanding and energy prices on the rise again, LNG carriers must meet entirely new requirements with regards to both design and operational efficiency. DNV GL offers unique capabilities in comprehensive performance optimization.
The worldwide LNG trade patterns are changing. Today liquefied natural gas is routinely transported across very long distances – typically from the USA or western Africa to the Far East. What is more, ship fuel prices, after years of decline, are on the rise again, while the pressure increases to keep the CO2 footprint in check. All this means that fuel efficiency plays a greater role than ever in keeping transport costs down and the ships attractive to charterers.
With this in mind, the Chinese shipbuilding company Hudong-Zhonghua wanted to get the best out of the design when planning its next generation of 174,000-cubic-metre LNG carriers. To leverage the latest expertise and technology, H&Z approached DNV GL for a joint development project. “DNV GL has rich experience and expertise in both the LNG industry and modern CFD technology for vessel performance analyses. We are very happy to work with this international leading class,” said Song Wei, Head of the R&D department at Hudong-Zhonghua. The operational profile for the ships was developed based on real-life AIS sailing data, which suggested a typical 60 per cent of sailing time spent in laden condition and 40 per cent in ballast, with speeds ranging between 15 and 19.5 knots.
In a first phase Hudong presented two design proposals: a slender, longer hull shape with a B1 beam (less than 46 m wide), and an alternative design with a wider, B2 beam (more than 46 m wide) at reduced length. To identify the most fuel-efficient concept, DNV GL undertook simulations with a standardized CFD setup in full scale. This procedure does not require application of traditional model test extrapolation methods since the fluid-dynamic properties are considered for the actual operating conditions. Both designs showed well-balanced performance between laden and ballast draught. For the anticipated operating profile, however, the B1 design exhibited a power demand that was approximately five per cent lower than that of the wider B2 variant, a penalty that could not be compensated by the benefit of higher displacement. Having achieved this much, the project partners were convinced that further hull design improvements would allow them to tweak efficiency by an additional three to four per cent.
Project phase two involved a dedicated, formal hull lines optimization to exploit the full potential of the B1 design. DNV GL’s ECO Lines service, which combines a fully parametric geometry model with computational fluid dynamics (CFD) and dedicated genetic optimization techniques, was the method of choice. The process began with a mutual definition of optimization targets and applicable design constraints. Then a dedicated parametric model was developed which served as a basis for generating hull shape variations. The process ensures that the ship forms derived are buildable while meeting the design constraints.
In this case constraints were applied to keep the displacement in ballast and laden conditions as well as the centre of buoyancy within tight limits. In addition a minimum propeller clearance was defined, and various hard points were added to allow installation of the LNG tanks.
Now the basic design was ready for computer-based optimization using DNV GL’s high-performance cluster of more than 7,000 CPUs. The geometry was generated for each design variant, and hydrostatic properties were analysed to check for intake and stability requirements. Design variants that met the requirements then underwent a performance analysis by means of computational fluid dynamics. More than 120,000 hull shape variations were looked at in the course of this project.
An item of special importance was the alignment of the propeller shaft lines. While many twin skeg designs feature inclined shaft lines to adapt to the local flow conditions, Hudong preferred parallel shaft lines to obtain a more compact machinery space. To investigate the detailed effects of the rotating propellers in the wake of the skegs, DNV GL utilized a dedicated software tool which uses fully viscous calculations to optimize the propulsion system, accounting for the rotational components of the propeller. Finally a configuration was identified that accommodated a parallel shaft line arrangement and showed the desired level of performance.
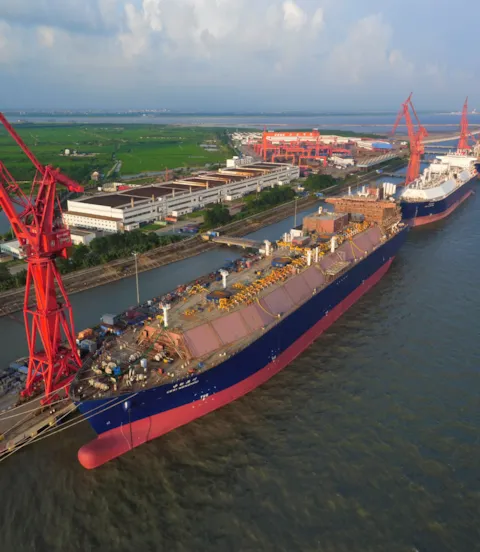
Energy efficiency optimization
Because of the complex nature of LNG carrier operation, the machinery and systems must be flexible and operate efficiently across the entire operational profile. Operational and demand profile models were developed using COSSMOS, a DNV GL simulation software tool. Hudong and DNV GL set the speed range parameters for laden and ballast condition ten to 20 knots. In addition, the engineer considered various non-sailing modes, including anchored unloaded, cargo loading, anchored loaded, and cargo unloading condition. Based on the operational profile, various re-liquefaction technology variants, fuel gas handling system configurations, and auxiliary engine economizers were subjected to techno-economic assessments using DNV GL’s COSSMOS tool. The results showed that AE economizer systems may bring better important overall efficiency improvement technology.
“We were very excited to see the final report, which showed that the expected improvement potential could be fully realized by this JDP,” said Song Wei, when the results had been reviewed. “We subsequently conducted model tests. We will be ready to offer our fourth-generation LNGC V2.0 design to our clients in the coming months – thanks to the great work done by DNV GL.”
Ling Deng
Ship Type Expert Gas Carrier and LNG fuelled Ships