LNGreen: sharing the way
Established to develop tomorrow’s LNG carrier through innovative use of today’s technology, the LNGreen joint development project is now drawing to a close.
Project partners DNV GL, Hyundai Heavy Industries (HHI), Gaztransport & Technigaz (GTT) and shipowner GasLog achieved significant improvements in LNG carrier design and efficiency in Phase I, focusing on hull hydrodynamics, cargo volume, reduced boil-off, and overall machinery and system efficiency. Compared to the base case, studies proved that an overall energy consumption improvement of approximately eight per cent depending on operating condition could be achieved.
Phase II was dedicated to further enhancing optimization potential and verifying results, including an increase of 25 per cent in operational efficiency from partial re-liquefaction, and a validation of the findings from LNGreen I for technologies such as dual-fuel auxiliary engines with economizers.
“Joint development projects (JDPs) are where we try out new ideas,” says Phase II Project Manager Daniel Nordås, Hydrodynamic Engineer at DNV GL Maritime Advisory. “Phase I delivered a lot of innovation, and we used Phase II to validate and refine these concepts, but also to encourage further investigation of potential uncovered in LNGreen.”
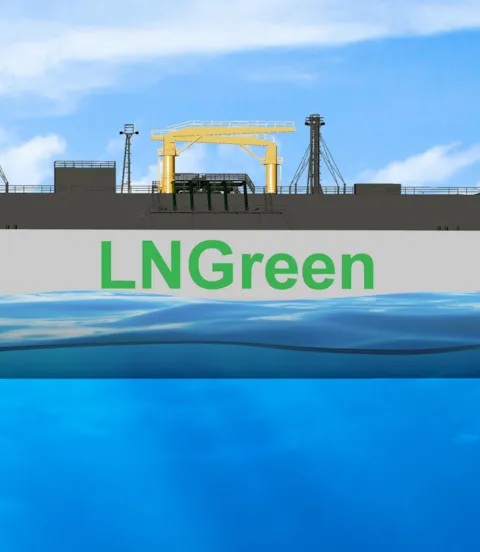
Open to improvement
The project focus was to combine accessible technology and existing knowledge in new ways, and that in itself required an innovative approach to sharing. “This particular way of working together required a different mindset,” says Nordås. “Compared to a typical JDP, there was more open discussion and sharing of knowledge. Each potential innovation was discussed freely.”
One notable example was the sharing of data and methodology. “Partners typically do not want to disclose the specifics of how they work, as this is their competitive advantage,” Nordås says. But in LNGreen, GasLog sent operational data to HHI and engaged with the yard in the design process, and DNV GL cooperated with HHI on advanced analyses such as added resistance in waves, in order to provide a more robust platform for design discussions and innovations.
“DNV GL’s primary role was to assure smooth cooperation between the partners, with a focus on finding new ways to use existing technology,” Nordås relates. “We provided design verification services and acted as a sparring partner, discussing both practical and technical matters, and potential class and regulatory issues.”
Representing tank design and manufacturing in the project, GTT has their own takeaway: “It is always a plus to have cooperated closely with leading industry partners, but in LNGreen we also gained valuable insight into shipowners’ requirements and priorities,” says GTT CEO Philippe Berterottière. “This further strengthens our credibility in future dealings with both yards and owners.”
GasLog’s motivation for participating in LNGreen was to discover and explore improved and innovative design solutions for the future LNG vessels, says a GasLog representative. “HHI was very accommodating in exploring new options to satisfy the project’s needs. HHI and GTT worked very closely together, and DNV GL contributed by validating technology and assuring compliance with class rules. All these efforts helped move the discussion forward.”
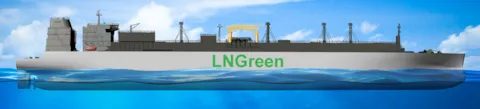
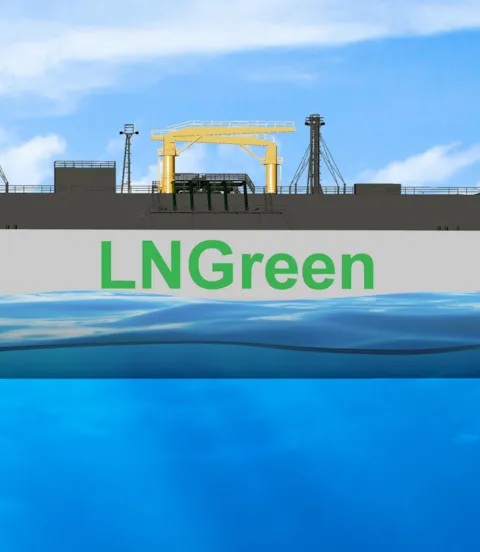
Sharing the benefits
Hyundai Heavy Industries also confirms their satisfaction with the overall results: “HHI is pleased with the good cooperation established between all partners in the LNGreen project. The partners have shared knowledge in new ways and achieved innovation that will benefit LNG shipbuilding and transport for many years to come,” says Project Manager Bumwoo Han from HHI.
Johan Petter Tutturen, DNV GL Business Director Gas Carriers, sums up: “LNGreen provided innovative insight into gas carrier design and operations, but the project also laid the foundation for increased trust and sharing between the partners. Now we look forward to sharing the benefits of all our efforts with the gas carrier industry.”