LNG-fuelled Newcastlemax for the “Green Corridor”
With DNV GL as project manager, a joint industry project (JIP) between key stakeholders operating in the “Green Corridor” bulk carrier trade between Australia and China has developed an LNG-fuelled Newcastlemax design as well as solutions for possible retrofits of dual fuel onto existing Newcastlemaxes. The solutions in this design are state of the art, yet well proven to make the design possible to order and build before the new sulphur limit of 0.5 per cent enters into force in 2020. The design had been presented at the Nor-Shipping exhibition in Oslo, Norway, in June 2017.
On 27 October 2016, IMO’s Marine Environment Protection Committee (MEPC) agreed to reduce the global sulphur emissions limit down to 0.5 per cent (from today’s 3.5 per cent) in year 2020, thus pushing global shipowners to make informed decisions on their fuel choice in the future in order to meet the stringent requirements. Among all possible fuel solutions that comply with the global sulphur emission requirements, many see LNG as the most forward-looking and practical fuel switch option.
The major charterers, shipowners and operators plying the Australia—China iron ore and coal trade route have for a while been contemplating the idea of developing the infrastructure for LNG as a marine fuel for the vessels operating this trade. With the IMO confirming its decision, these stakeholders, together with Australia’s major LNG supplier Woodside, as well as ship designer SDARI and class society DNV GL, decided to come together to develop a suitable LNG-fuelled bulk carrier solution.
To enable the quick ordering of these vessels, possibly for delivery already before the IMO sulphur requirement enters into force in 2020, the project partners decided on an evolutionary approach rather than a far-fetched, revolutionary approach. For example, the choice of engine type would therefore be of the rather conventional type, albeit dual fuel, having capability to carry both conventional fuels as well as LNG, as opposed to relying on less-tested technologies such as gas turbines or similar options. Since LNG is known to be a substantially cleaner fuel option than most other options presently available, the LNG-fueled vessels operating between Australia and China will market the trade route as the “Green Corridor”.
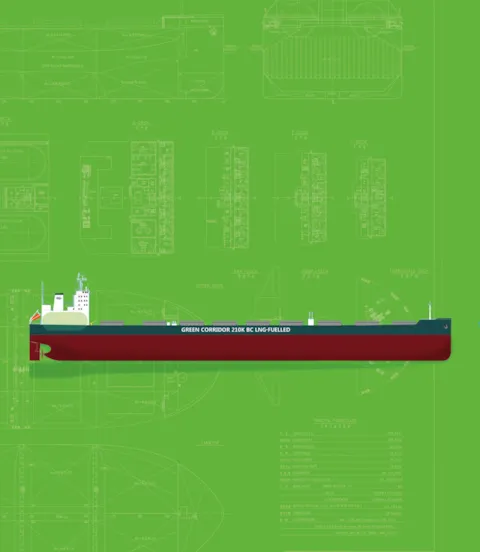
“Green corridor” JIP partners
The stakeholders active in developing the LNG-fuelled infrastructure in the iron ore and coal trade between Australia and China came together to conceptualize an LNG fuelled Newcastlemax bulk carrier. The partners represent the whole value chain around the “Green Corridor”, including energy supplier Woodside, mining majors and cargo owners/charterers Rio Tinto, BHP and FMG, major shipowners MOL and U-Ming, and finally ship designer SDARI and classification society DNV GL:
- BHP
- DNV GL
- Fortescue Metals Group Ltd (FMG)
- Mitsui O.S.K. Lines, Ltd.
- Rio Tinto
- Shanghai Merchant Ship Design And Research Institute (SDARI)
- U-Ming Marine Transport Corp.
- Woodside Energy Ltd.
“Green Corridor” JIP objectives
The key project objectives were:
- To assess the business case of LNG as fuel for Capesize bulkers operating in Australia under various pricing scenarios including alignment of the bunker supply chain
- To develop an efficient and practical LNG-fuelled Capesize concept design to a level where it will get an Approval in Principle (AiP) and where owners may start to negotiate orders from yards based on this design
- To bring together key stakeholders to address common challenges and position Australia at the forefront of developments in LNG fueled shipping
Each partner participating in the JIP benefits from working together. Importantly the partners are shaping the future of bulk carriers that will trade in this route. Shipowners and operators MOL and U-Ming provide design inputs through fleet operation experience. Charterers BHP, FMG and Rio Tinto want their supply chain to be robust and sustainable and thus influence the size and scale of fleet operations as well as the suitability of the ships to fit their terminal capacities and constraints in an optimal way. Designer SDARI gets direct feedback from the end users not only on the efficiency of their design, but also helps make their design more viable for actual operations. Based on the operational feedback, LNG bunker supplier Woodside can make informed decisions for their own bunkering development as well as help the other partners design ships that will fit optimally with the available bunkering facilities.
DNV GL has for many years built up its competence and capacity as a thought leader in LNG as fuel for the maritime industry, and now further expands on this in its capacity as both project manager and one of the key contributors to the “Green Corridor” JIP. In its role as a classification society, it is imperative for DNV GL to work closely with key industry partners to get first-hand feedback on its rules and design standards, and to help shape the future world fleet towards a greener footprint.
“The JIP partners decided early on that a Newcastlemax bulk carrier (about 210,000 dwt) would be the most flexible design for the trade route between Australia and China, since it would cater for both iron ore and coal as cargo.
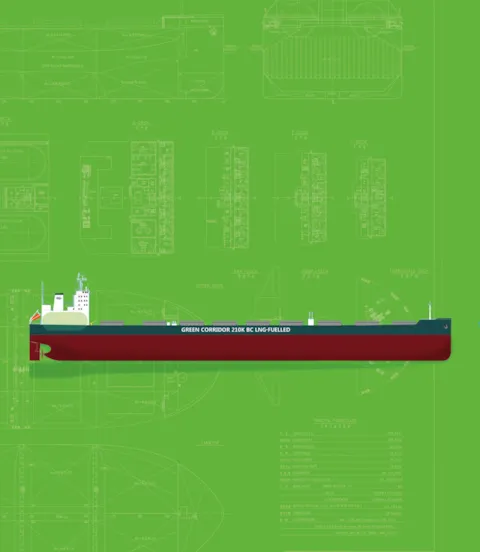
LNG-fuelled bulk carrier – retrofit or newbuild?
The first question raised in the JIP was: “What would be more cost-effective – having an existing bulk carrier retrofitted to run on dual fuel (conventional as well as LNG fuel), or to build a new, dual-fuelled bulk carrier?” Hence, a study was conducted to compare the cost implications of both these options.
The study resulted in quantifying the actual difference in opting for retrofit versus newbuild as a solution for the “Green Corridor”.
The study revealed that a retrofit option is possible from a technical point of view, but would allow less capacity for the LNG fuel tanks, and hence less operational flexibility, and the retrofit option is also significantly more expensive due to the higher capex in the engine installation and the corresponding shipyard costs in comparison to a newbuild. Also, from an operational and cost point of view, the location of LNG fuel tanks is more challenging for the retrofit option, as the tanks would need to be placed on the aft deck. Hence, the question is omit rather whether there is need for more vessels operating this route or whether there already exists enough capacity for this trade. Taking into account other environmental regulations that have already or will soon enter into force, such as the Ballast Water Convention and NOX Tier III requirements, the partners find it likely that a newbuilding option may be attractive. The following therefore focus mainly on the evaluations done for the newbuilding design, although a concept design for a retrofit option was also developed as part of the JIP.
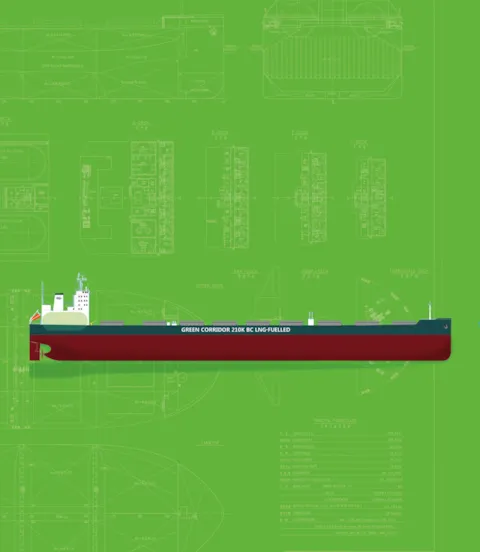
Design considerations
The LNG fuel tank is the single most expensive component of an LNG fuel system, and so the optimal selection of tank size is of vital importance. The larger size the more flexibility in trade route and bunkering options, but it also results in the highest investment cost and the biggest technical challenges (such as finding space on board the vessel, trim and stability challenges, structural reinforcement to take the load of the tank and fuel, etc.).
Operational trade routes between Australia and China were analysed for the cruising distance, typical ports called, weather impact (based on AIS data from vessels trading the route over the last years), safety margin, engine efficiency, etc. Based on the analyses of the listed factors that typically affect fuel consumption, a cruising range from 10,000 nautical miles to 24,000 nautical miles was studied.
A mid cruising range of 14,000 to 18,000 nautical miles showed the highest number of runs for a round trip i.e. from the load port to discharge port and back. LNG fuel tank size of about 6,000 m3 was found to be optimal for the said cruising range, with bunkering in Australia for the round trip. The analyses were carried out mainly for the iron ore trade, but also allow for the flexibility on some of the major coal trading routes. The said tank size not only caters for the Australia–China trade, but also has built-in flexibility for some occasional longer voyages.
Several locations for the LNG fuel tank were considered: midships, in front of the engine room, on the aft deck, etc. After several iterations and comparisons, locating the LNG tanks as close to the engine as possible was found to reduce the risk induced by long cryogenic pipelines and pressure drop. It also reduces the need for building other additional risk mitigation options and, last but not least, it reduces the costs of the cryogenic systems.
With due considerations on operational flexibility as well as trim and stability and structural strength (longitudinal bending moment and shear forces), an optimal solution was found to place the two LNG fuel tanks under the superstructure of the accommodation area, where it would be surrounded by steel structure and A-60 insulation, and of course completely separated from the accommodation area and cabins. This way, the fuel tanks will be partly submerged into the engine room. This is a rather innovative design, which caters both for proper protection of the fuel tanks, while also ensuring proper fire protection towards the accommodation, and at the same time it utilizes the engine room space so that it does not reduce the cargo carrying capacity (not even for volumetric cargoes such as coal).
Dual-fuel engines were quickly decided upon by the JIP partners, due to their robustness in offering operational redundancy, combined with sturdiness and several suppliers offering mature solutions.
Both low-pressure and high-pressure engine types have been included into the design to allow for maximum flexibility, since both options have their own pros and cons. However, it is important to note that the design is fully NOX Tier III-compliant, and thus the high-pressure engine option is also fitted with an exhaust gas recirculation (EGR) system.
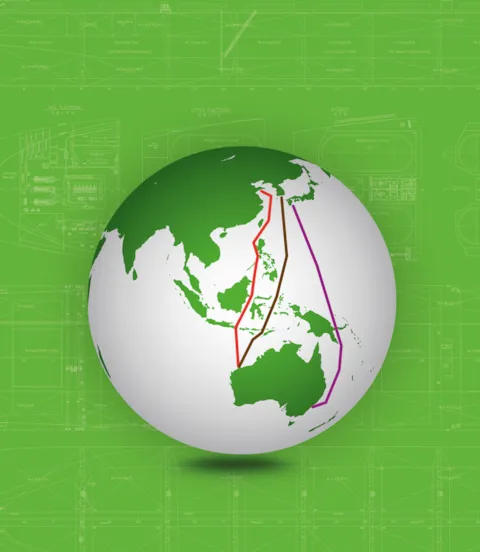
Economic considerations
One key driver for the “Green Corridor” is of course to provide more environmentally sustainable transportation in compliance with future environmental regulations. However, it also needs to be sustainable from a commercial point of view, and therefore the operational costs for an LNG-fuelled solution was investigated in detail in the JIP. The main conclusion is that in the long term, the operating costs are predicted to be substantially lower than for a conventional solution. The expected reduced fuel costs and longer overhaul intervals are the main contributor for reduced OPEX, and indicate a quite attractive payback period of less than ten years.
An important part of the JIP has been to conduct a financial feasibility study for the LNG-fuelled Newcastelemax design. It was carried out based on a wide range of possible capital cost, operational cost and sensitivities to LNG prices and that of low sulphur marine fuel oils as well as a high-level bunker supply chain assessment.
It devised the most cost-efficient solutions for the design and mapped out payback periods under different pricing conditions, and showed an encouraging payback period of less than ten years in the scenario deemed most realistic, whereas a payback period down to six to seven years was predicted in a more optimistic scenario.
The outcome of the study reinforced the belief in LNG as marine fuel for the vessels operating in the identified trade route, and it also helped understand key issues that impact vessel design and the business model for both ship operators and the LNG bunkering suppliers.
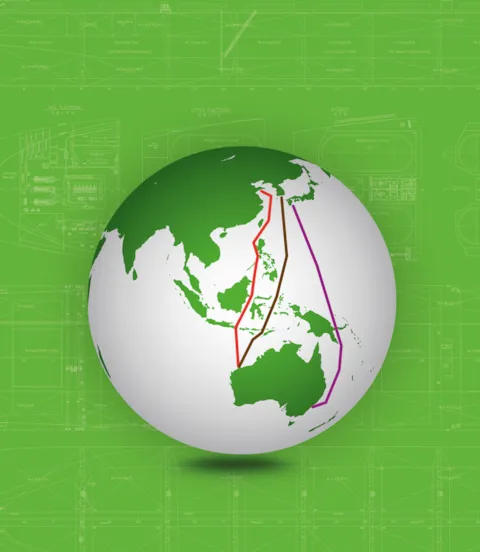
Newcastlemax concept design
World-famous Chinese ship designer SDARI developed the design of the 210,000 dwt Newcastlemax bulk carrier based on their highly energy-efficient Green Dolphin design. This design has already been highly optimized for minimum hull resistance under various realistic operating conditions, including operating profiles considering realistic combinations of speed, trim, draught, etc.
As mentioned, the selection of engine type, LNG fuel tank size/capacity, location and tank type were some of the main decisions carefully reviewed in the project. Whereas an evolutionary approach was selected, one of the key innovations involved in this design was the position of the Type C tanks. Through several iterations, it was identified that two tanks, each placed above the engine room but submerged from the main deck, would give an optimal balance between cost, operational flexibility and safety.
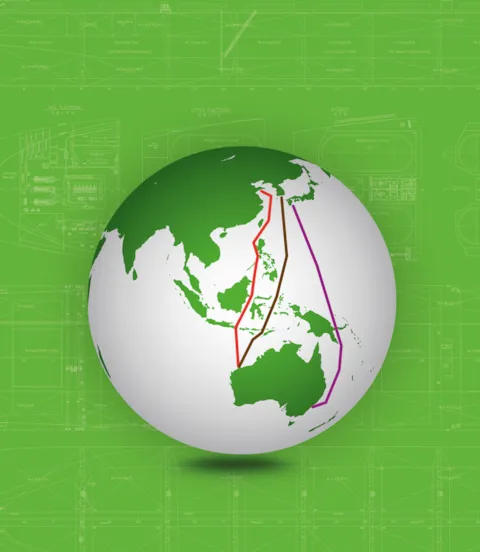
A future-proof design
A high-level hazard identification (Hazid) exercise was carried out as a risk assessment approach to identify the key hazards that may occur due to on-board LNG storage and operations. All partners participated in this exercise, which proved very useful to share a common understanding of the challenges at hand and what technical solutions could mitigate the risks.
Major incidents that can cause potential hazards, their frequency of occurrence and consequences were mapped out. A list of actions which could be mitigation measures, recommendations or considerations were tabulated for each of the potential hazards.
These action items were later taken into consideration by SDARI in their proposed design to enhance the safety of the design against different elements. The refined design developed by SDARI is now in the process of being submitted to DNV GL for a thorough review according to class rules and applicable regulations. Provided all factors have been satisfactorily considered, DNV GL will issue so-called Approval in Principal for the design.
Thus, in this manner, the JIP aims to arrive at a Newcastlemax design which is in line with charterers’ requirements, shipowners’ and operators’ requirements as well as in full compliance with international rules and regulations.
All vessels sailing in designated emission control areas (ECAs) currently need to comply with the 0.1 per cent sulphur regulation, and after 2020 all vessels sailing globally will need to comply with the 0.5 per cent sulphur regulation. Some ECAs also impose strict regulations on NOX emissions. All the above urge shipowners to investigate alternative options for compliance for their vessels based on the operational profile, trade pattern and investment cost. LNG as a fuel is a single-system solution for emission regulation compliance, ensuring compliance with both the SOX and NOX regulations.
The new, innovative Newcastlemax design developed in the “Green Corridor” JIP, offers unique solutions for cost-efficient, safe and flexible operations. By gathering key stakeholders representing the wider value chain of iron ore and coal transportation, a more robust, commercially viable and safe LNG-fuelled bulk carrier design has been developed to a stage where it is ready to serve as the outline specification for newbuilding orders.