Flexibility makes the difference
Continuing a long-standing, highly productive working relationship, Oshima Shipbuilding and DNV GL have developed a state-of-the-art design for a 65k, open-hatch general cargo carrier.
High efficiency and flexibility are the keywords that best describe the purpose of a new joint development project between Oshima Shipbuilding and DNV GL. Oshima, well known as a specialist in open-hatch carrier design, was envisioning a modern, high-performance ship utilizing the best available technologies and adapted perfectly to current market demand. In addition to their extensive combined experience, Oshima and DNV GL used input from major owners as well as extensive market research accounting for fleet profiles, trades and cargoes.
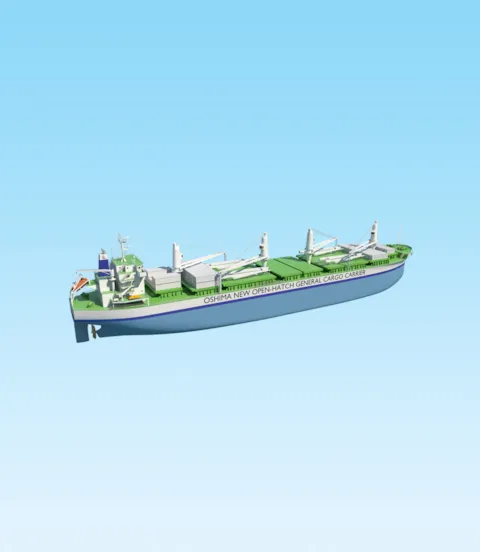
Ship size and cargo hold configuration
The design is intended for a wide range of project cargoes and packaged goods, such as the carriage of lumber, wood pulp, coils, ingots and carriage of other major and minor bulk cargoes. As cargoes increase in quantity, diversity and size, open-hatch general cargo carriers often carry a variety of goods during the same voyage, which requires many port calls along the route. Flexible loading options and excellent utilization of the available cargo space were therefore top items on the project agenda, along with high operational efficiency and emission compliance.
The deadweight and main dimensions were chosen based on market demand and an assessment of the current fleet and order book, accounting for port limitations, trade patterns and cargoes. Considerations were also made as to find the optimal hydrodynamic performance for the given size. The design features a high cubic and deadweight capacity at a shallow draught, enabled by an increased breadth without compromising performance. This allows the ship to enter a large number of ports. It has eight box-shaped cargo holds with full-width hatch openings, including two long holds for larger project cargoes. Holds No. 2 to No. 7 have piggyback-type hatch covers while holds No. 1 and 8 feature folding covers. Rapid cargo handling is ensured by four all-electric jib cranes, a cost-effective selection offering flexible loading compared to the more expensive gantry cranes.
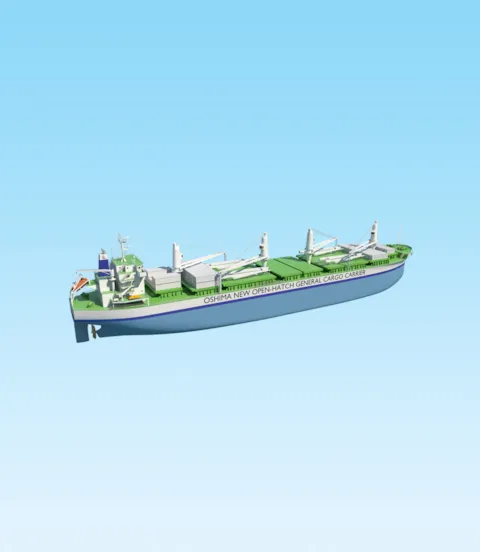
Composite tween decks
The ship is specifically designed for the use of tween decks to maximize space utilization. Holds 2, 3, 6 and 7 can be compartmentalized in this manner. For weight reduction Oshima, DNV GL, COMPOCEAN and IKNOW Machinery jointly developed innovative composite tween deck panels, each made of a single skin GFRP (glass-fibre-reinforced plastic) top plate bonded to corrugations, which in turn are bolted to the end plates. These composite tween decks are 50 per cent lighter than steel versions without sacrificing any of the functionality, service or safety. The developers accounted for load carrying capacity, dimensional stability, impact resistance, reparability, environmental effects, vibrations, wear and fire safety. Benefits include significantly shorter port handling time, reduced maintenance costs and a simple, cost-effective manufacturing process. A full-size prototype was produced and tested and the design concept has received approval in principle (AiP) from DNV GL. The AiP confirms that, while some details and design solutions need further clarifications, the innovative composite design concept is feasible for application in bulk carriers and cargo carriers.
A similar approach was taken for the hatch cover design where an existing joint development of DNV GL and Oshima was adapted for the current project. In 2013 DNV issued an AiP for the composite hatch covers followed by Panama flag approval for fire safety.
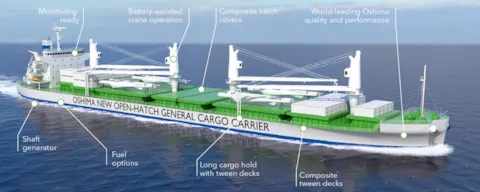
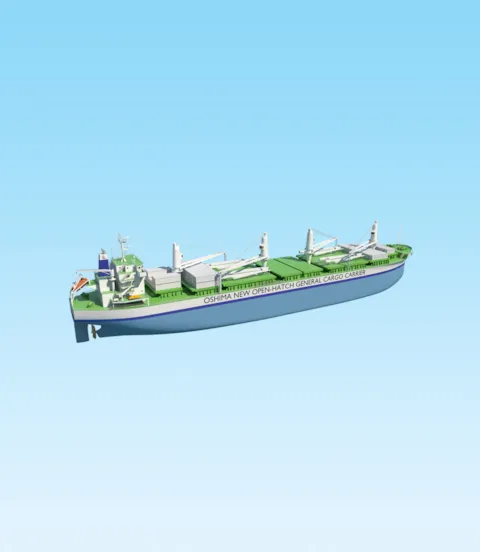
Energy-efficient power supply system
A feasibility study by DNV GL has investigated the fuel-saving potential of battery pack-assisted crane operation. This found that a hybrid system can save up to 20 per cent of annual fuel costs for crane operations, resulting in an estimated six- to nine-year investment payback time where the range depends on if the auxiliary engines are run with LSFO or MGO as fuel. With the battery pack absorbing peak loads, one or two auxiliary engines running close to optimal load – instead of the usual two or three – can supply enough power for crane operation. This result in a potential reduction of genset running hours of 50 per cent. When lowering cargo, the cranes can regenerate energy and feed it back into the batteries. An additional DC/ AC inverter will allow the batteries to be connected to the main switchboard.
Furthermore, investigations of a large number of comparable vessels revealed frequent operation at low loads, confirming the opportunity to improve the overall main engine running performance and thus potential to improve the annual fuel consumption. DNV GL has found that an optimized six-cylinder, two-stroke main engine running on LSFO in combination with a PTO/PTI (power take-off/power take-in) shaft generator could reduce annual fuel costs by up to 10 per cent and maintenance costs by more than 30 per cent. An additional 1.5 per cent savings can be achieved through utilizing the battery in operations where generator sets are kept running at low load due to redundancy. The additional investment will pay for itself within a period of four to eight years, depending on auxiliary engine fuel type and price.
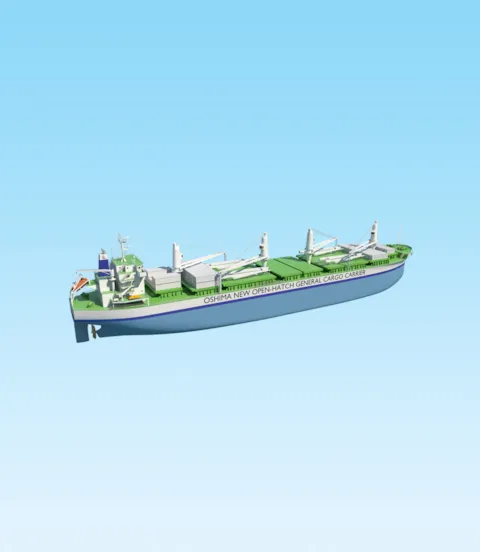
Energy-efficient power supply system
To meet current and future emission limits, the Oshima design offers various options for different fuel strategies. Apart from the baseline LSFO version with exhaust gas recirculation (EGR), available options include HFO with a SOX scrubber and EGR/SCR, LNG, and an innovative Super Eco Fuel which is currently being developed by Oshima and several industry partners. A financial comparison of the available options has been done, giving an initial indication if, or under which conditions a scrubber and the new fuel type are financially attractive compared to the LSFO option. Within the assumptions of the comparison, the scrubber solution provides shipowners with a positive outlook for a return on investment. The new fuel type option also seems favourable from an economic point of view.
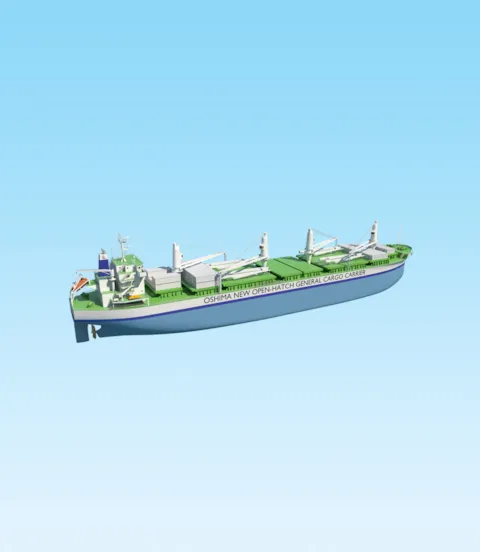
Significant potential
This new Oshima concept design delivers an excellent combination of characteristics for the varying trade and cargo requirements representative for the open-hatch general cargo segment. “We believe this new ship design will be very useful for our customers. The ship has great cargo flexibility and several new technologies for general cargo carriers have been implemented, such as composite tween decks, a PTO/PTI shaft generator and batteries,” says Tatsurou Iwashita, Deputy Yard General Manager at Oshima. Both Oshima and DNV GL agree the design offers a highly attractive option to owners and operators in the openhatch segment, combining well-known technologies that are currently available, making this a design ready to order while it includes features little used today but with significant potentials.
Says Morten Løvstad, DNV GL’s Global Business Director for Bulk Carriers: “This new concept design of an innovative, open-hatch general cargo carrier is a good example of how cooperation between industry partners can benefit the maritime industry. The use of low-weight composite material for bulk carriers and general cargo carriers has been an area where both DNV GL and Oshima have done R&D for many years already, and I am pleased to see that this concept has now reached a level where it can be applied in commercial design, ready for order. Also, the use of hybrid solutions for the crane operations is a technology I think will be common in most of the future bulk carrier designs. Finally, I am excited about the new “Super Eco Fuel” developed by Oshima – provided sufficient availability of bunkering and technical feasibility of engine performance can be assured, this new fuel may have a significant potential as marine fuel!”