Flexibility for changing markets
With its latest orders for next-generation LNG carriers and FSRUs, the BW Group has again demonstrated its flexibility in adapting to a changing market environment. The newbuilding orders reflect a continuous search for efficiency gains whilst maintaining full focus on safety and operational excellence. Supported by in-house newbuilding and technical management teams, BW’s recent growth initiatives have already paid off in attractive charter contracts.
At BW, the commercial team and a dedicated group of technical experts from their in-house newbuilding department keep a close eye on market requirements and seek solutions to address an increasingly dynamic market environment in LNG shipping and infrastructure. In developing projects, BW utilizes the long-standing technical experience gathered from numerous newbuilding projects since the company was established, alongside operational experience from managing one of the largest fleets of LNG and LPG carriers in the world. Each new project benefits from a growing and deepening pool of knowledge where new designs are continuously optimized for safety, efficiency, maintenance and the environment.
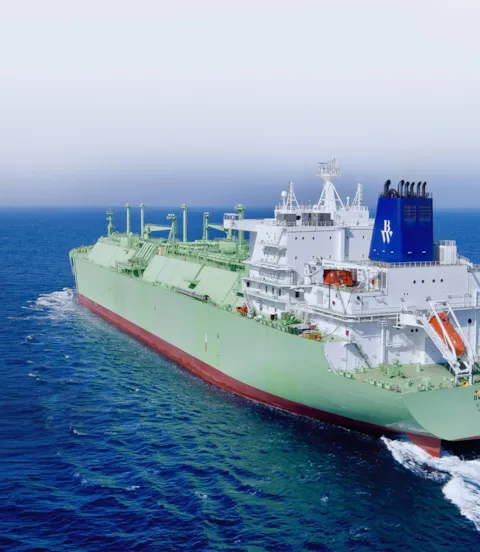
BW’s growth initiatives are set against a backdrop of an LNG industry constantly seeking efficiency gains, and BW’s strategy is to be at the forefront of this development. To adapt to the changing market environment, BW has recently ordered five next-generation LNG carriers as well as three FSRUs, all classed by DNV GL.
All our ships are built for maximum efficiency, safety and reliability,” says Petter Larssøn, Vice President, Gas Solutions and LNG Shipping, BW LNG. He emphasizes, “Our aim is to be at the forefront of efficiency developments not only for today, but also in the development of lasting solutions which will be competitive over time”. With this in mind, the in-house newbuilding team makes numerous modifications to the original design. “We have many preferences when tailoring newbuilding designs and may apply as many as 800 to 1,000 changes to a yard design, from small to large, in order to include lessons learnt, ensure operational flexibility, and include new technological developments,” Kasper Winroth, LNG Manager at BW LNG, explains.
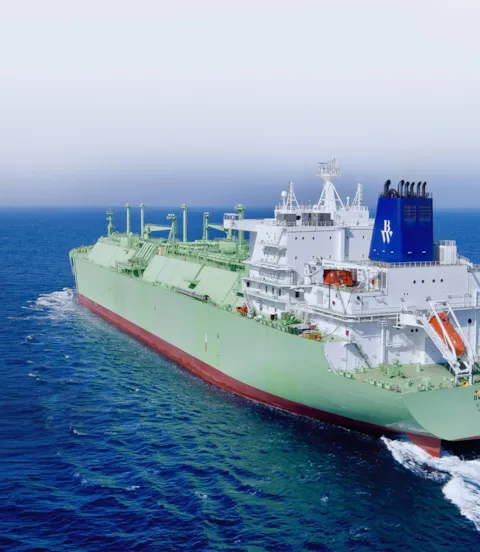
Open dialogue in design development
The technical preferences range from careful selection of equipment makers to improving redundancy and efficiency through to enhancing the design to ensure the crew can fulfil their tasks. “We believe these efforts yield results, through optimizing the design we ensure that operations and maintenance will be much more efficient, which provides the best economics for us and for the customer,” Larssøn underlines. Having an in-house newbuilding team and a large gas carrier fleet facilitates sharing experiences and solutions with key yards and suppliers across all disciplines involved in ship design. The newbuilding team is in constant dialogue with shipyards and equipment makers to evaluate new developments, improvements or products. This includes close cooperation with partners such as DNV GL.
“Having an open dialogue on what goes on in the industry and continuously working on optimizing the designs is very important for us,” Larssøn comments. “We have a longstanding relationship with DNV GL and they understand our business and our constant push to evolve and change in line with the dynamic industry environment. DNV GL has been involved in many processes during the newbuilding phase, looking at equipment, instrumentation, automation, digitalization and more, and supporting us in the constant pursuit of operational excellence and operating best-in-class vessels. Moving into future concepts like digitalization and automation will get increased focus going forward. We are looking at alternatives for operations and maintenance, which could involve innovations such as the use of drones for tank inspection, which will save costs and improve safety,” he adds.
The recent LNGC and FSRU newbuilding orders were placed before firm charters were lined up amid changing market requirements. “We have taken some newbuilding positions ahead of charters/contracts to time deliveries and benefit from attractive yard pricing. This allows us to meet the expected market requirements,” Larssøn explains. “This is especially important in the FSRU segment, where the lead time of projects is often very short and you cannot offer a solution to the client without an available asset”, he adds.
So far, these decisions have paid off: BW’s first FSRU, the BW Singapore, was chartered immediately following delivery for the EGAS project in Egypt, with a world-record five-month implementation time after contract signing. The second FSRU, the BW Integrity, was chartered out on a 15-year contract in Pakistan shortly after delivery. Similarly, the two MEGI LNG carrier new-builds delivered in Q1 2018, BW Tulip and BW Lilac, are both committed to charters. Furthermore, FSRUs offer an interesting risk mitigation option by doubling as fully tradable LNG carriers. “In case of time gaps between delivery and start-up of an FSRU project, the vessels can sail as LNG carriers with competitive features such as large size and relatively efficient fuel consumption,” Winroth points out.
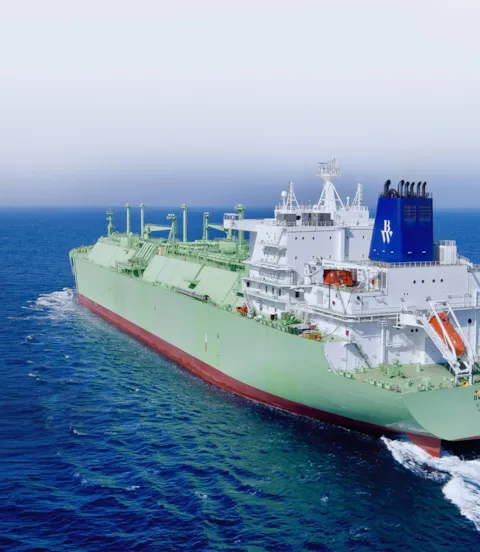
Flexible and capable FSRU newbuilds
When BW LNG launched the FSRU projects, the newbuilding team first optimized the designs so the vessels would be competitive for most projects worldwide. One of the key parameters is regasification reliability and efficiency, especially when these vessels are deployed in connection with large infrastructure projects. “One of the major developments in FSRU technology is increased regasification efficiency and capacity compared to five or ten years ago. The size of FSRUs has also increased to provide more storage space and accommodate cargo from all types of incoming LNG vessels,” Larssøn explains. With a capacity of about 170,000 cubic metres, these FSRUs are big enough for LNGCs of nearly any size whilst ensuring highly efficient operation and fast send-out. “We aim to design FSRUs that fit most projects worldwide, focusing on safe, reliable, efficient operation and flexible capacity,” Winroth explains. All of BW’s FSRUs are based on seawater heating, either direct or via a glycol intermediate loop, to regasify the LNG in the most energy-efficient way. The capacity of the regas plant is tailored to location-specific conditions. Equipped with efficient four-stroke DF engines from Wärtsilä and MAN, the BW ships offer regasification with a minimum of environmental footprint.
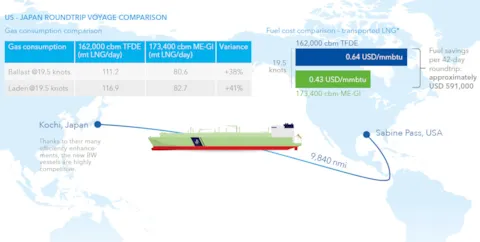
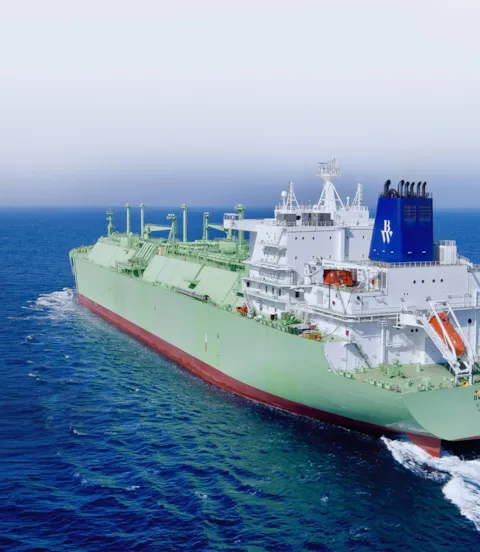
LNG vessels for the future
Another project the BW LNG newbuilding team has been working on is the development of next-generation LNG carriers that will attract clients in an ever-changing market with increased demand for flexibility and efficiency.
For the series of five vessels ordered from DSME, the new-building team and its partners again utilized their extensive LNG-specific operational experience to achieve significant improvements over existing vessels.
“The big driver in LNG shipping is reduction of the unit freight cost,” Larssøn points out. “You can reduce the unit freight cost by building larger vessels with lower fuel consumption and boil-off rate.” 174,000 cubic metres is the size BW LNG prefers as it is highly flexible; 180,000 cbm ships may also be considered in future.
The fuel consumption of the new LNG carriers is some 30 to 40 per cent lower than that of DFDE/TFDE, and even better when compared with steam propulsion, thanks to the slow-speed two-stroke dual-fuel engines. The ME-GI engine offers reduced specific consumption, improved propulsive efficiency and increased fuel flexibility. Allowing almost any mix of gas and liquid fuel, the engines give the charterer a wide range of options. Apart from the larger size and lower fuel consumption of BW’s next-generation LNG carriers, the third big efficiency improvement is the significant reduction of the boil-off-rate (BOR), achieved by combining a low-BOR containment system with a reliquefaction system working in tandem with the ME-GI fuel gas supply system. This ensures the best reliquification efficiency in the market, compared to independent reliquefaction systems. BW also places great emphasis on minimizing the environmental footprint of its ships. Lowering emissions to air and sea is a continuous effort at BW. Of course the vessels will comply with the relevant emission regulations. This can in part be achieved by reducing fuel consumption; in addition, the latest newbuilds have an EGR system on the main engine to reduce NOX emissions to Tier III levels while reducing the amount of waste water that is discharged to sea, compared to an SCR system.
To comply with the Ballast Water Management Convention, BW LNG has opted for a combined electrolysis and filter system that comes with both IMO and USCG approval.
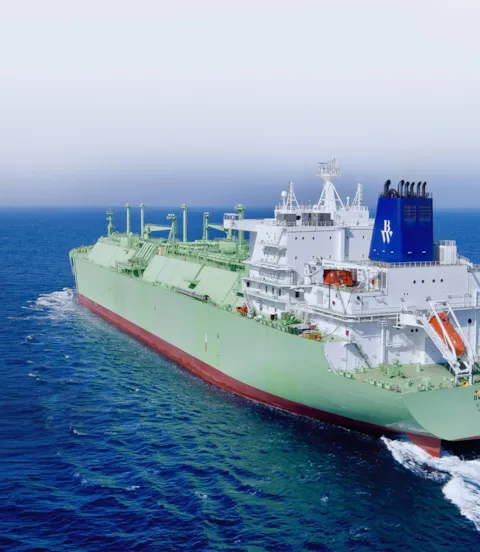
Zero harm is paramount
BW has a zero-harm policy and continuously works towards the ambitious goal of eliminating safety incidents entirely. The company believes that one aspect is to design vessels to reduce risks; a second one is to educate the crew, the yards and the suppliers to eliminate hazards and safety incidents, both during construction and during operation. BW has its own yard teams who supervise construction and work together with the suppliers and partners executing its projects. Experts from DNV GL are also present on site to support the supervision and make sure the work is performed in a safe manner. Cooperating closely with customers as well as partners such as DNV GL, BW constantly strives to live up to its zero-harm goal. “This is about changing behaviour, processes, procedures, training, communication, management, leadership, on-shore and offshore operations, and practising a safety culture that ultimately pays off by keeping people safe,” Winroth points out.