Equipment Criticality Analysis supports successful recommissioning
Idle ships inevitably deteriorate. Preserving and maintaining the thousands of components on board with limited budgets, time and resources is challenging. However, an effective maintenance programme is an assurance of a safe and successful return to operation.
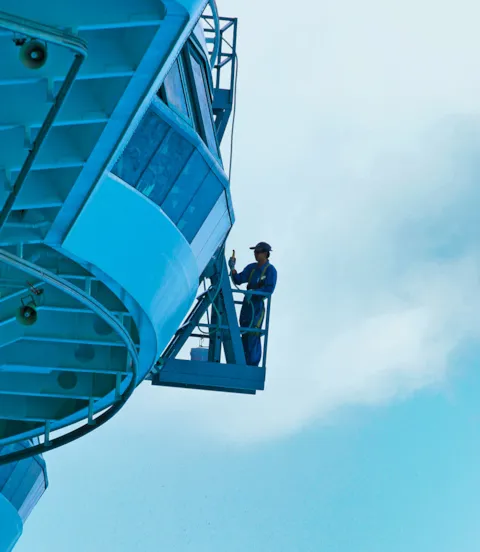
Assessing economic risks
Since cruise ships are much more complex than merchant vessels, the requirements for cold lay-up are quite different in this ship segment. “There are many challenges associated with an idled cruise ship,” Frode Brattum, Senior Technical Manager at Fred. Olsen Cruise Lines, points out. “The biggest challenge is the assessment of the economic risk.” In terms of preserving everything on board, it is difficult to strike a good balance between minimizing costs during lay-up and minimizing losses when resuming operation, he adds.
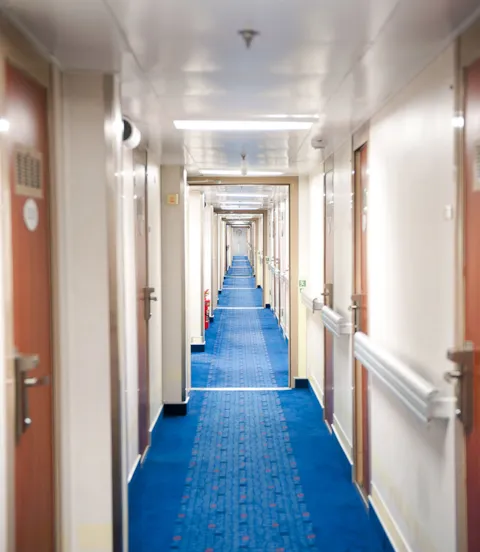
Support for ship preservation and recommissioning
To help owners prepare and implement a well-structured preservation and recommissioning plan, DNV offers its Equipment Criticality Analysis service. “The purpose of this methodology is to identify the best and most economical maintenance and preservation strategy, prioritizing work and optimizing resources under reduced crewing,” explains Richard Tao, Discipline Director and Senior Principal Consultant at DNV. “In particular, our ‘Getting Back in Service’ product seeks to minimize the risk of compromised business due to breakdowns, cancellations, crew discomfort or unpleasant guest experiences when a ship starts sailing again, and to facilitate a timely and cost-efficient restart.”
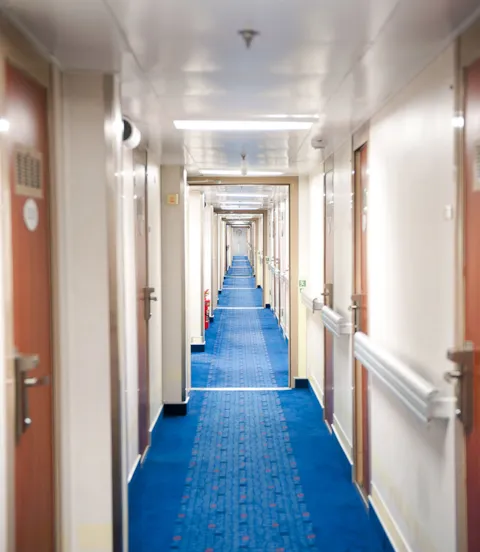
Qualitative assessment of everything on board
An Equipment Criticality Analysis involves a qualitative assessment of a ship’s amenities, equipment and systems when it lies idle for an extended period. In a comprehensive five-step process and several workshops, a DNV expert will guide the vessel manager and crew in defining a lay-up and preservation strategy. “By professional judgement, the consequences of the predictable deterioration of various equipment over time is assessed and ranked in order of the seriousness of the consequences on operation, safety, the environment and maintenance costs,” says Tao. “Best practice, industry experience and manufacturer recommendations are key inputs to the analysis. The result of the assessment is an equipment criticality classification list covering all technical details and management procedures.”
A cruise ship has hundreds of different systems on board, each of which needs to be taken care of in a very specific way to maintain its function and integrity. Critical machinery such as engines, pumps and hydraulics may stick or corrode if not started up and lubricated regularly. Gaskets can dry out, rubber hoses can crack. On the other hand, some equipment just needs to be greased, covered and left alone.
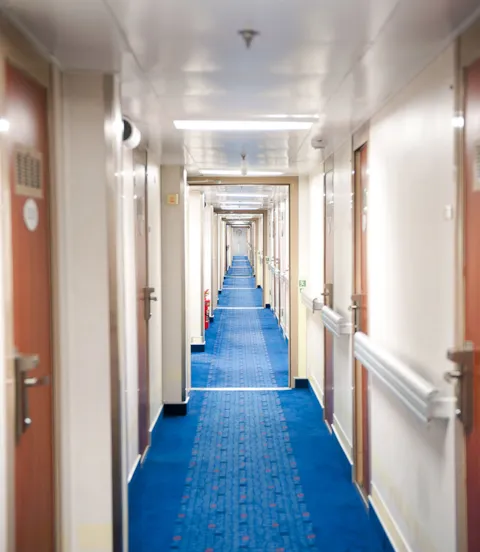
Hotel facilities require extra attention
The accommodation and public-health-related areas are an aspect unique to cruise vessels, Tao points out. “Sundries, provisions, linen, artwork and plants are best moved to warehouses on shore. Failure to properly manage the hotel facilities will result in microbial growth, mould and dust accumulation. Foul or stale smells can accumulate which are difficult to eliminate. Accommodation areas, life support systems and tanks need to be cleaned, flushed and sanitized. Maintaining a minimum of ventilation with controlled humidity is essential. What is more, the ship’s fire and flooding safety systems need to be fully operable. And the exterior of a vessel can quickly deteriorate, showing black streaks and rust patches. It is important for a cruise line to ensure a clean appearance of its ships, which are very visible to the public. In order to manage all this, the owner needs to have in place a supervision management team, security, agreements with maintenance personnel, a watch regime and a sound maintenance schedule.”
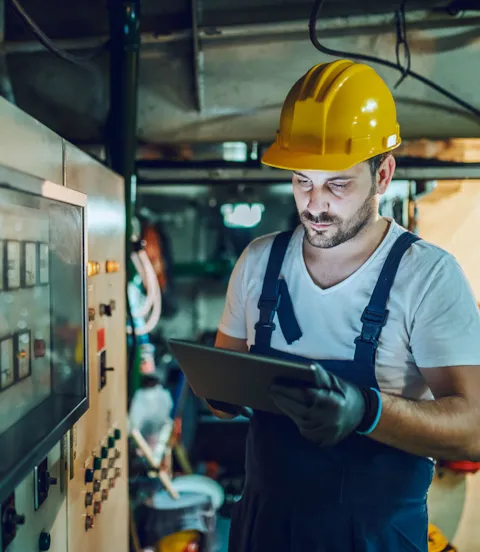
Well-chosen, protected location
Fred. Olsen Cruise Lines decided to take their fleet of four cruise ships to a protected location close to the division headquarters in the UK. “The place we chose outside Edinburgh has a non-tidal basin separated from the Firth of Forth by a lock. Our four ships all fit into this basin and could be kept alongside,” says Frode Brattum. “This reduces their exposure to the elements and the risk of damage significantly. We also have a lot more flexibility with our staff because the people in charge of monitoring the vessels can move between them.” One of them is kept “warm”; this is where the crew members taking care of the vessels are accommodated, Brattum explains. “These are members of each ship’s regular crews, who know their vessels well. Every day they perform a number of checks on their ships and carry our repairs if necessary.”
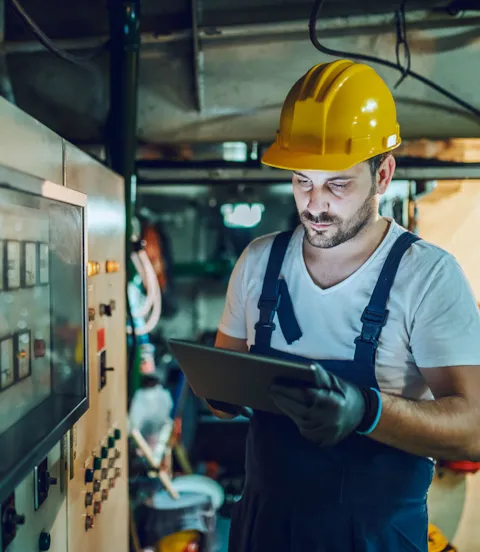
Addressing air humidity
The biggest concern is humidity and air quality on board, says Brattum. “Air moisture will interfere with everything. If you do not control air quality, not only will all the electronic equipment be ruined but the artwork as well. The wallpaper will come off, and there will be mould everywhere, especially in a moist climate like that of Scotland.” Fred. Olsen have placed dozens of dehumidifiers on their vessels to protect everything that could not be taken to shore facilities.
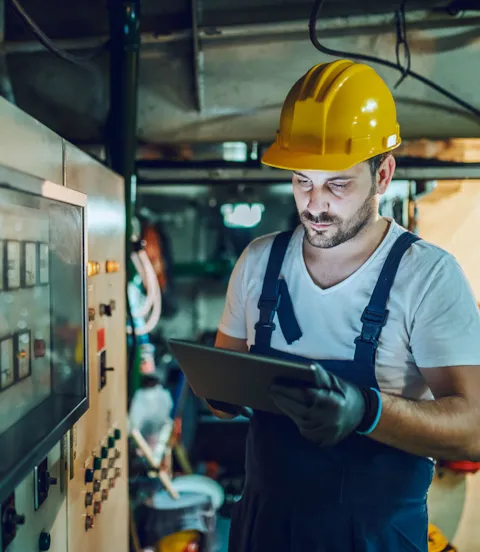
Ensuring a smooth recommissioning process
With a sound, risk-based plan in place, starting up a ship after it has been idle should not be unlike taking delivery of a newbuild, says Richard Tao. “The hotel will be ready to receive supplies, and all systems and machinery will be ready to operate. A significant benefit enabling a smooth start-up is a systematic, comprehensive list of what equipment has been subject to what kind of preservation, and what needs to be removed, restored or replaced.
” DNV can step in and provide expert advice at any point in the preparation or recommissioning process, stresses Tao. Fred. Olsen Cruise Lines were in constant dialogue with DNV as the pandemic took its course, and the issue of preserving the ships was part of that conversation, adds Frode Brattum. “The DNV verification, which took about one month to complete, served to assure us that we had taken the right decisions.” To his surprise, holding the related workshop digitally instead of physically on board did not complicate matters. “We were able to cooperate very well electronically. It was easy to deliver the service digitally, which was a great benefit in our eyes.”
Fred. Olsen Cruise Lines are taking a phased approach to reactivating their fleet. They will begin taking passengers again as of 5 July 2021. The fourth and last ship, Braemar, is scheduled to take passengers in April 2022, says Brattum.
Paal Johansen
Global Cruise Ship Director
- Darryl Brooks – Shutterstock.com
- Evikka – Shutterstock.com
- DNV
- Dusan Petkovic – Shutterstock.com