Ensuring satisfactory aft stern tube bearing lubrication performance
DNV GL’s long-standing efforts to ensure safe performance of aft most propeller shaft bearings continue. The class society has recently updated its oil lubrication acceptance criteria to differentiate between environmentally acceptable lubricants (EALs) and mineral oils in terms of their ability to form a reliable lubricant film.
In recent years an increasing number of costly stern tube bearing failures have been reported across multiple ship segments and sizes. These failures have coincided with the increased uptake of environmentally acceptable lubricants (EALs) after the December 2013 introduction of regulations prohibiting the use of mineral oils in all oil-to-sea interfaces on board commercial vessels trading in U.S. waters. Many of the failures are wiping damages at the aft end of the aft stern tube bearing occurring with fresh oil. While the majority of the breakdowns were caused by a combination of factors, the performance of the lubricants themselves has been drawn into question by the industry.
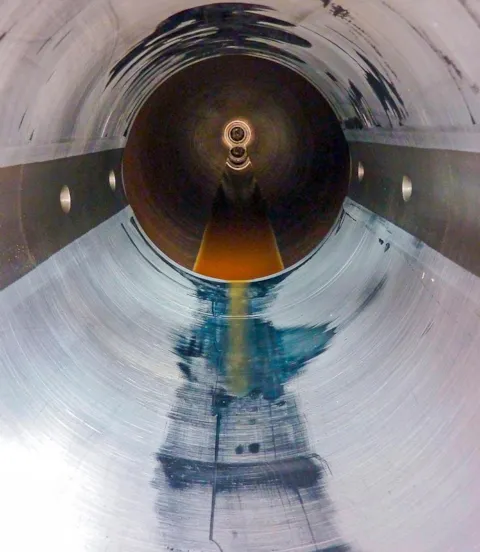
New eco-lubricants raise questions
To better understand how EALs perform compared to traditional mineral oils commonly used in stern tube bearings, DNV GL initiated a joint development project together with the marine insurers The Swedish Club, Norwegian Hull Club, Skuld and Gard (1). The aim of the project was to map out potential differences between the lubricants’ physical properties that determine their oil film load-carrying capacities, with a focus on how the lubricant viscosity is influenced by parameters such as temperature, pressure and shear rate. Operational issues and potential long-term degradation issues have not been covered by the study as the majority of the observed failures occurred with fresh oil. Laboratory testing has been carried out by and under the guidance of leading tribology experts at the University of Sheffield in the UK and at INSA Lyon in France.
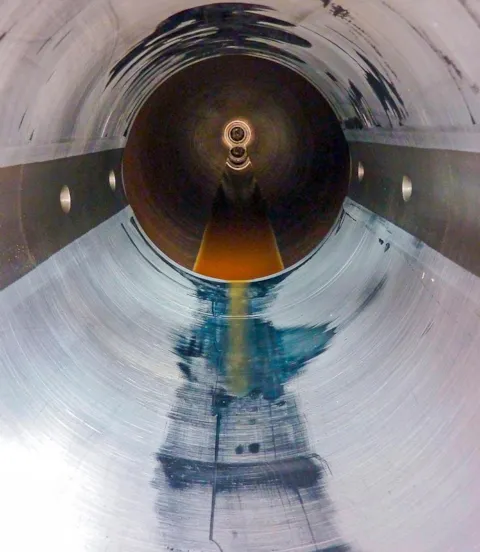
Understanding the physics
In order to decide which influence parameters to focus on when investigating EALs, it is essential to understand the major factors that affect the performance of an aft stern tube bearing. “The physical forces acting on propeller shafts under highly variable vessel-operating conditions result in a complex array of challenges that must be overcome to achieve a satisfactory shaft alignment and ensure adequate lubrication of the aft stern tube bearing,” explains Øystein Åsheim Alnes, Principal Engineer at DNV GL Group Technology and Research. “Over the past years several EEDI-driven vessel design features have helped improve overall vessel energy efficiency but have had an unwanted secondary impact: there is no doubt that bigger and slower-rotating propellers tend to reduce the safety margins of the aft stern tube bearing. Likewise, various hull and propeller wake optimization features have been found to do the same for certain operating conditions. As the maritime industry works towards achieving IMO’s ambitious goals for reducing its environmental footprint, this trend towards more energy-efficient ships needs to continue. Therefore, we at DNV GL have acknowledged that a more sophisticated approval methodology for stern tube bearings is required.” The industry-standard approach of only evaluating the bearing projected pressure and the simplified shaft vs bearing relative slope for static conditions is no longer adequate.
DNV GL has built unrivalled expertise in this field over decades, merging knowledge from class, independent advisory projects and dedicated research and development activities. This accumulated know-how has enabled the classification society to develop state-of-the-art design rules for shaft alignment, including a highly detailed approach to verify the aft stern tube bearing design for both static and running conditions. The calculation method for the minimum shaft-rotational speed at which hydrodynamic lubrication of the aft stern tube bearing is ensured was introduced in 2013. Better known as the “DNV GL oil lubrication criteria”, it is based on a quasi-empirical solution of the Reynolds equation for journal bearings. It accounts for the challenging conditions that are typical for stern tube bearings, such as very uneven load distribution and extensive misalignment between shaft and bearing. The calculation method aims to ensure hydrodynamic lubrication in the areas exposed to the maximum bearing pressure, setting a limit for the minimum allowable continuous operational shaft speed at dead slow ahead and engine maximum continuous rating (MCR).
Originally, the specified kinematic viscosity was the only input parameter needed to define the required stern tube lubricant to be used. This was based upon the fact that almost all installations used various engine crankcase oils in the stern tube. Regardless of make, these traditional mineral oil lubricants are very similar with regard to their viscosity properties and load-carrying capabilities. The first phase of the EAL study was set up to investigate these viscosity properties and to quantify any potential differences between the new biodegradable lubricants and the traditional mineral oils.
While investigating the viscosity properties of various EALs available on the market, the study has so far identified two main aspects where the tested biodegradable lubricants behave differently when compared with a reference mineral oil: pressure-related and temperature-related viscosity properties. Additionally, one of the EALs are found to display shear thinning properties at high shear rates. Detailed results are explained in our slideshow "Main findings of EAL study", which is linked below the article.
EAL study conclusions
“The overall conclusion we can draw from the JDP Phase 1 results is that (new and non-degraded) EALs provide safety margins equivalent to those of mineral oils in most operating conditions,” Alnes summarizes. “However, there are transient conditions involving high oil film pressures and/or low oil temperatures where EALs will have a reduced load-carrying capacity.” The vast majority of stern tube bearing failures in recent years occurred in the same type of transient conditions, e.g. during hard manoeuvring at high ship speeds (high pressure), during mooring trials (low temperature and high pressure), and when operating with a partly submerged propeller (high pressure). Thus, the observed damage picture fits well with the findings of the study.
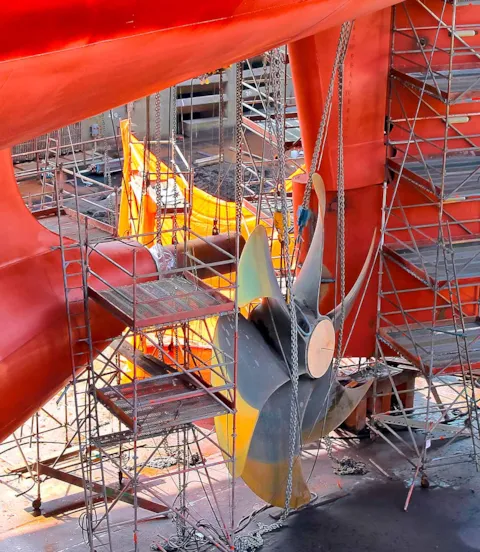
EAL study results prompt update of DNV GL shaft alignment rules
To ensure that the aft stern tube bearing operates safely within the hydrodynamic lubrication regime, several parameters must be kept in mind - in particular the viscosity of the lubricant and the local peak pressure. “The tests performed during the EAL study revealed that under certain operational conditions the viscosity properties of biodegradable lubricants differ from those of mineral oils,” Alnes explains. Our rules are the only ones which account for both local pressure and viscosity, and we have incorporated the results of the EAL study into our class regime. It has been found that applying a viscosity factor for non-mineral oils of 0.75 will bring the safety margins to the required level. This means that the outcome of the EAL study can be applied directly to the DNV GL lubrication criteria, and that the required safety margins can be maintained regardless of lubricant type.” The update is included in the July 2019 rule edition (not retroactive for vessels with older applicable DNV GL rules).
To maximize the margins regarding safe oil film thickness, the layout of the aft stern tube bearing should be optimized to have a good fit towards the propeller shaft across a range of operating conditions, such as increased contact area and reduced peak pressures for example. This can typically be done by choosing a bearing design and alignment that allows for a very low minimum speed, ensuring hydrodynamic lubrication in the conditions given by the DNV GL lubrication criteria. A multi-slope bearing design is normally the most efficient way to achieve this. Furthermore, DNV GL offers two voluntary class notations, Shaft Align(1) and Shaft Align(2), as an option for owners who want to ensure even higher safety levels for their ships’ stern tube systems.
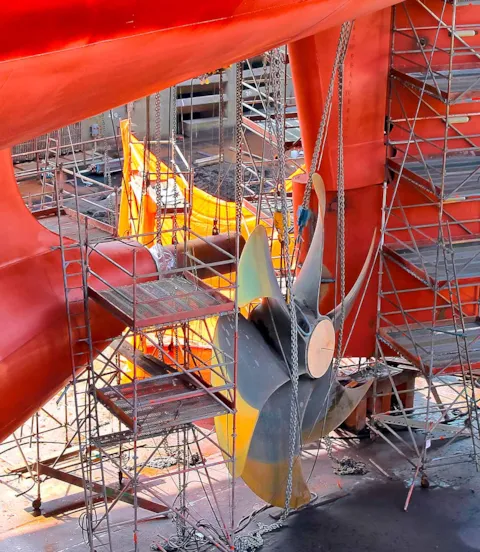
What’s next?
The DNV GL-led EAL study is now moving into the next stages where oil-film-forming capabilities, mixed/boundary lubrication behaviour and lubricant degradation will be scrutinized further.
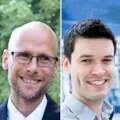
Erlend Hanssen Nervold | Øystein Åsheim Alnes
Principal Engineer Machinery and Systems | Principal Engineer Digital Class and Services
- Key image - ©Nightman1965_stock.adobe.com
- Left side 2 - Keith Michael Taylor_Shutterstock.com
- Text image 1 - DNV GL
- Left side 3 - nicknick_ko_stock.adobe.com