Eco-friendly shuttle tankers for Norway
With its new “E-Shuttle” concept, developed in cooperation with Wärtsilä, Teekay opens up a new chapter in setting ambitious environmental standards for shuttle tankers.
As a major player in the shuttle tanker sector, the Teekay Group with its affiliated company Teekay Offshore has always embraced forward-thinking ideas and concepts. Ever since the Norwegian authorities imposed restrictions on environmentally damaging volatile organic compound (VOC) emissions in 2003, Teekay has explored many options for reducing emissions from its shuttle tankers.
The development of their latest innovative, eco-friendly shuttle tanker concept “E-Shuttle” started in 2016. Amongst other new features, the design concept incorporates several of Wärtsilä’s new technologies. Its annual emission reduction potential is estimated at up to 42 per cent, with fuel consumption reduced by up to 22 per cent compared to traditional shuttle tankers.
An initial order for two Suezmax-size, DP2 shuttle tankers based on the new concept was placed at Samsung Heavy Industries (SHI) in July 2017, followed by two more in November 2017. SHI will supply the fully compliant, DNV GL classed vessels in 2019 and 2020, respectively. The 130,000 dwt shuttle tankers are destined for service in the North Sea under Teekay’s existing agreement with Statoil and many other customers.
“This is another important milestone for Teekay Offshore’s shuttle tanker franchise since it further strengthens our position as the leading provider of shuttle tanker services in the North Sea,” commented Ingvild Sæther, President and CEO of Teekay Offshore Group. “Our customers require a reliable, long-term solution for securing offtake services from over 15 oil fields in the North Sea and, therefore, these state-of-the-art newbuilds demonstrate our ongoing commitment to our customers,” Sæther continued. “What makes me particularly proud is that these newbuilds will set new standards for both fuel consumption and CO2 emissions.”
The new shuttle tankers will operate on both liquefied natural gas (LNG) as the primary fuel, and a mixture of LNG and recovered volatile organic compounds (VOCs) as secondary fuel. Environmentally harmful VOCs are produced in a gaseous state from evaporation occurring in the oil cargo tanks. That new mixture enables shuttle tankers to travel from the oil fields on their own waste gas rather than releasing it into the atmosphere. This will reduce both emissions and bunkering requirements considerably.
The fuel mixture will cut NOX emissions from engine exhaust gases by more than 80 per cent to a level below IMO Tier III limits. Since LNG contains almost no sulphur, SOX emissions will be eliminated almost entirely, and particulate emissions will be reduced by more than 95 per cent.
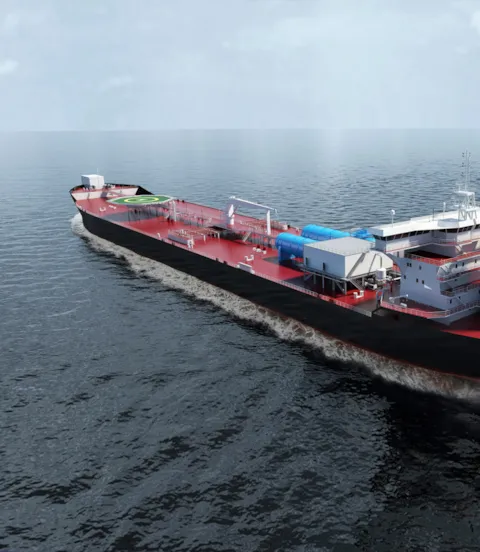
Utilization of waste VOCs
During operation, traditionally designed shuttle tankers produce high levels of emissions, in particular VOCs which are typically released during loading, storage, and transport of crude oil.
Since more than 50 per cent of Norway’s VOC emissions occur during storage and loading of crude oil, stringent emission reduction regulations have been implemented which apply to all shuttle tankers receiving crude oil from offshore processing platforms on the Norwegian continental shelf. VOCs evaporating from the cargo tanks during loading must be captured by a VOC recovery plant.
“Teekay has long experience operating VOC recovery modules in the North Sea,” explains Sæther. “With more stringent requirements to reduce VOC emissions and the use of LNG as a primary fuel, we are now able to burn the liquefied VOCs, previously seen as a byproduct with limited value, as fuel in our vessels. This solution creates value for our customers as well as potential environmental benefits. Our experts have spent significant amounts of time developing this new technology together with Wärtsila and believe the additional enhancement will provide future value.“
The new generation of VOC recovery plants will comply with the more stringent government requirements expected to take effect from 2030. The heavier hydrocarbons are converted into liquid VOCs (LVOC) using several compression and cooling phases, and stored in a tank on deck. The lighter hydrocarbons, referred to as surplus VOCs (SVOC), are not liquefied. The main component of SVOC is methane gas that will be burnt in a gas turbine for electricity generation, delivering twice the efficiency of a traditional boiler and steam generator arrangement.
From a typical 850,000 bbl crude oil load from a North Sea platform, the plant will recover 100 tonnes of LVOC and 10 tonnes of SVOC. By reusing those VOCs as a fuel, the annual emissions can be reduced by 42 per cent. Assuming approximately 32 loads per year, this means cutting the CO2 discharge from 43,000 down to 25,000 tonnes. An average 100 tonnes of recovered LVOC per load could provide up to 30 per cent of the total fuel consumed by the new shuttle tankers. The new concept allows 100 per cent of the recovered LVOC to be used as fuel for electric power generation. Teekay has therefore replaced the conventional two- and four stroke engine configuration with a fully electric main propulsion system and four stroke dual-fuel (DF) generator sets that also increase flexibility and avoid functionality overlap. To achieve full SECA and NECA compliance, the new shuttle tanker will be equipped with Wärtsilä’s fuel gas handling system that includes a bunkering station for gas mode operation.
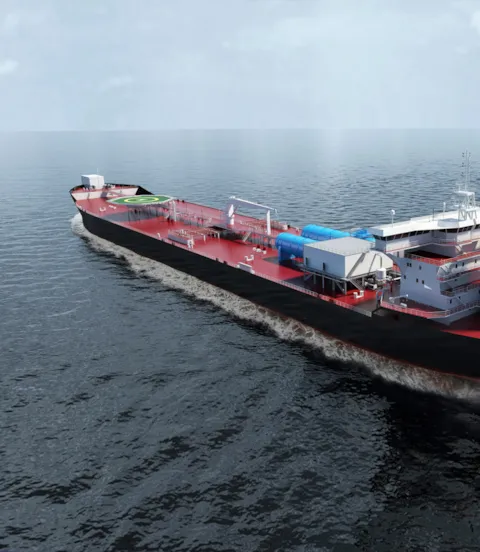
Operational flexibility
The new power distribution system is part of Wärtsilä’s low-loss hybrid (LLH) system, which uses batteries to store excess energy generated and enables more fuel savings through peak load shaving and added overall system redundancy while minimizing the impact of a failure during DP operation.
The battery storage system will handle dynamic load variations when the gensets are operating at optimum load, eliminating the need to start further gensets to buffer transient load variations. The new shuttle tankers are the first ships of their size to be equipped with a battery storage system for improved efficiency during transit operation.
Highly dependent on their DP capabilities, shuttle tankers can benefit from a hybrid power system in more ways than most other cargo ship types, and while the DP system of a traditional shuttle tanker consumes 60 per cent of thruster power, these new ships will require only 40 per cent. This further improves their fuel efficiency and enhances their manoeuvring capabilities. Built-in system redundancies will ensure resilience when unexpected incidents occur that might otherwise have severe consequences in the harsh environments where these vessels will operate
The new hybrid system also has a direct positive impact on main machinery operation, resulting in fewer running hours and consequently lower maintenance time and costs. The total installed power on board was reduced from 26 to 23 MW. Apart from the required trial speed of the vessel, the size and functionality of the power plant is determined by the power requirement during DP operations. While a traditional electrical distribution system could lose more than 50 per cent of installed power and several thrusters, the low-loss hybrid system can lose only 25 per cent of the installed power and no more than one thruster. Together with the electric propulsion system, it reduces the required total mechanical installed power by 14 per cent, increasing the overall fuel performance compared to traditional power distribution concepts.
As a total result of the new concept, the total energy consumption will decrease from 110 GWh to 75 GWh per year compared to a traditional shuttle tanker.
“Working together with the world’s most experienced yard and suppliers in the shuttle tanker segment is one of the key success factors in this project. SHI has integrated all systems into a very efficient hull. Brunvoll supplies all propulsion systems and reduction gears which need to be integrated effectively into the rest of the vessel systems,” Sæther describes the collaboration of the project partners. “As our classification partner, DNV GL supports us in achieving compliance in important aspects such as the LNG/ VOC mixing and battery solutions, which are the main environmental drivers of this project.”
Catrine Vestereng
SVP and Global Business Director for Tankers