Drones herald in new era of inspections
Visual inspections and steel thickness measurements are key elements of renewal surveys. Preparing ships for these activities is time-consuming and costly. DNV GL now offers a fast-track solution using drones.
DNV GL has been using camera-equipped drones in surveys since 2016. The concept, the technique and the equipment were developed by the surveyor team in Gdansk in response to customer enquiries. A traditional survey requires rafting, roping or staging so the inspection personnel can reach all relevant structural elements. Rafting takes additional time to ballast and de-ballast the vessel; both roping and rafting often require voyage surveying. Setting up staging can even take days.
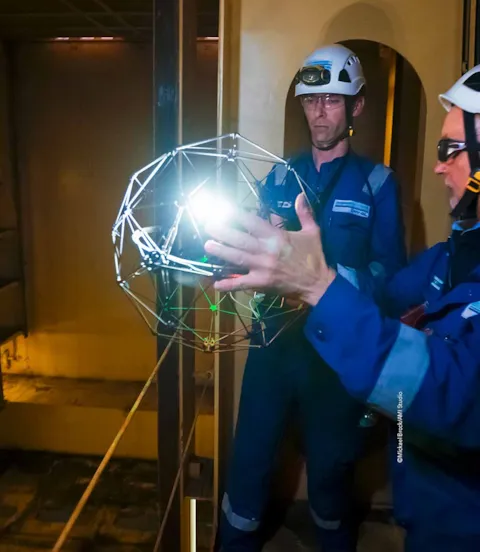
New tools for remote surveys
This disproportionate effort caused owners to inquire about alternative methods. In addition, staging often damages surfaces and coatings that must be repaired. In certain situations owners have to hire subcontractors providing rope access techniques, an especially hazardous type of work.
These conventional inspection methods put ships off-hire for weeks, which means lost income. Logically owners have an interest in keeping these times as short as possible. This led to the idea of using drones. “We started the drone project in 2015 to make surveying smarter, more efficient and economical for the owner, and safer for surveyors,” says Tomasz Oledzki, Head of Section Fleet in Service (FiS) Poland at DNV GL ‒ Maritime. The first step was to attach a high-resolution camera to a drone so surveyors could take a close look at hard-to-reach places. Several off-the-shelf drone models were tested. The team ultimately chose a medium-sized model for interior inspections, and a larger, more powerful one for outdoor inspections where wind can make positioning and controlling the drone more difficult, for example on offshore platforms.
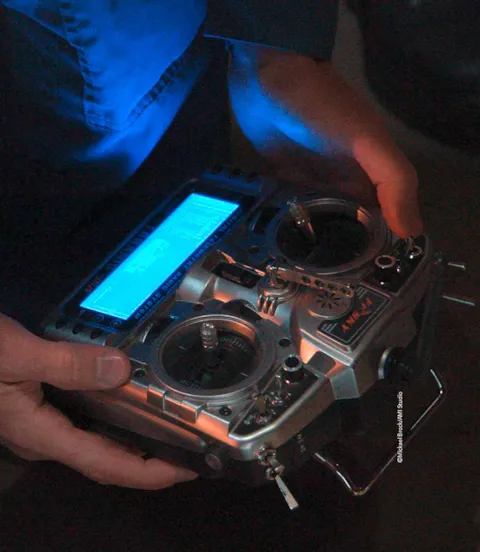
A new dimension: thickness measurements
“We now have three years’ experience performing camera-assisted visual inspections on ships and offshore structures using drones,” Oledzki continues. “But our customers expect more. They would like us to cover the full scope of inspections using this advanced technology, including thickness measurements. So in mid-2018 we decided to venture into this field and began developing a flying thickness measurement system. We built several prototypes and finally arrived at a design that satisfied our requirements.”
An attachment frame was engineered in-house by the Gdansk team in an iterative process including repeated practical testing. Its design is compact and ‘universal’, allowing surveyors to interchange the close-up inspection camera for the ultrasonic measurement head on a drone at any time, or attach the frame to another drone in case the original one is damaged. This standardization minimizes the amount of equipment surveyors have to carry when travelling to a ship, especially when dispatched by helicopter. “Reducing the amount of luggage was actually our key objective when developing this system,” stresses Oledzki.
What is more, key parts of the attachment frame are made by the DNV GL team on a 3D printer, which means the team can now manufacture any number of identical frames in a repeatable process, whether for their colleagues at other DNV GL offices or for spare parts.
Today we can say we have the capability to offer owners the full package of drone-assisted remote survey services including close-up inspection and verification of the thickness measurements.
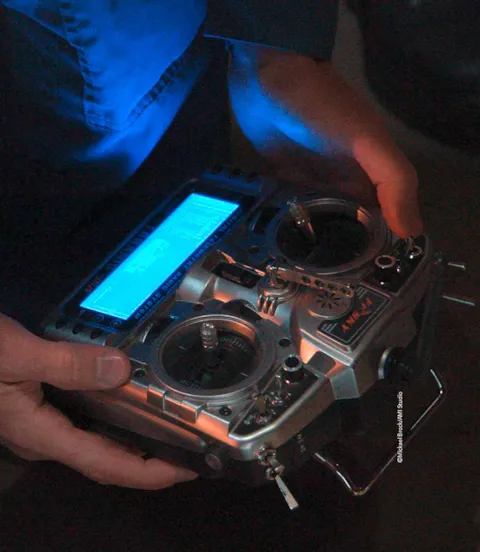
Bottom-line value for owners
“We have successfully tested the new thickness measurement drone on an MPV, some bulk carriers and this shuttle tanker,” says Oledzki. “The results are very positive – the system works well and delivers reliable data. Today we can say we have the capability to offer owners the full package of drone-assisted remote survey services including close-up inspection and verification of the thickness measurements.”
Alba adds: “We see a great opportunity to accelerate the survey process and minimize off-hire times; what is more, we can actually perform some inspections during the voyage of a vessel when cargo spaces are accessible. This is of great value to owners and operators.”
The biggest challenge the Gdansk team faces is to convince ship and cargo owners that the new methods delivers good and reliable results, says Alba. But the response from customers is excellent: “The owners for whom we have performed drone surveys to date have been very satisfied, and in many cases they were outright surprised how quickly and efficiently inspections can be done, and how little owner involvement is required to provide access to the structure. Whereas in the past, the surveyor had to be physically taken to the structural element to be inspected, the drone now ‘brings the structure to the surveyor’ for real-time inspection.”
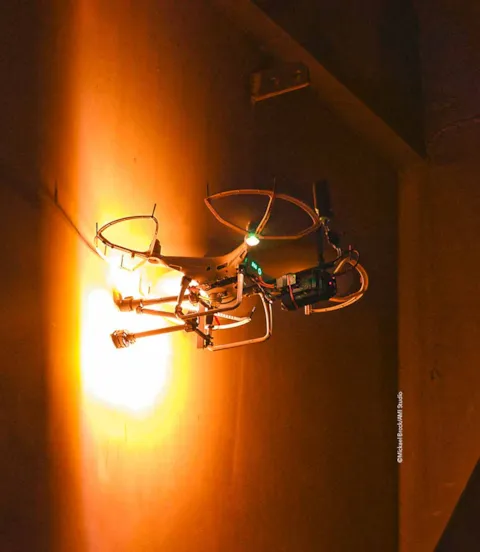
Limitations and opportunities
Yet owners should not foster unrealistic expectations, Leszek Alba cautions: “The critical point is the condition of the vessel interior.” Oledzki explains: “When we receive a request from an owner for a drone inspection, we take our equipment on board and first assess the condition of the vessel to see whether thickness measurements can be done with the drone. If the coating is intact and the surfaces are clean, we can get good visual inspection results and high-quality thickness readings. If the condition of the vessel is not suitable for ultrasonic thickness measurements, we can still use the drone with a mounted camera to perform a visual inspection.”
“Drone or not, it is impossible to take ultrasonic measurements on corroded steel because the measurement head is unable establish direct contact with the steel to get a reading,” stresses Alba. “Ultrasonic measurements are suitable to confirm the intact condition of structures. Our drone inspections serve the purpose of verifying the good condition. They are ideal for renewal surveys of younger vessels that are five to ten years old.”
The classification rules require a wide range of thickness measurements, most of which are typically performed by subcontractors. “It is important to note that our measurements are only supplemental to what the contractors are doing,” Alba points out. “We only access structures that cannot be reached by conventional means. We use drones to perform close-up surveys and to verify and confirm that a ship is structurally in good condition as required under class rules. The drone accelerates this spot-checking process dramatically so we can accomplish it within a single visit. We can even perform it during a voyage or port stay.” Wherever conditions are detected that warrant further investigation, traditional access using staging is unavoidable, he adds; but when the drone survey shows that everything is in good condition, this expense can be avoided.
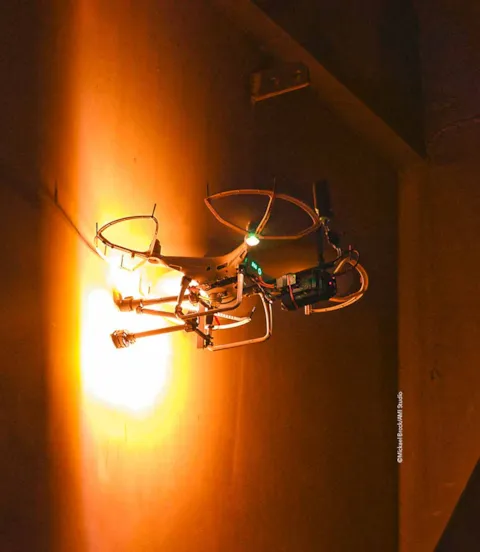
An evolving technology
Younger tankers, MPVs and bulk carriers are the primary targets of DNV GL’s drone survey offer. Oledzki says that conceivably drone measurements could be extended to cover the full scope of thickness measurements at some time in future. And that is by no means all this technology could accomplish. “The last step of this development could be autonomous drones performing close-up inspections and thickness measurements,” says Leszek Alba. “They could either navigate based on sensor and navigational algorithms or using an electronic model such as the ‘digital twin’. This would enable the surveyor to stay outside, simply watching the computer screen and letting the drone do its work independently.” A research programme in Oslo is underway to investigate these possibilities, and there are even scientific studies in progress to identify potential contactless thickness measurement technologies.
As for the present, incorporating thickness measurements in drone surveys is already a big step, says Alba: “Today we have gathered enough experience and solid results to know what we can achieve in assessing the condition of structures. Autonomous drones will essentially do the same but with less operator involvement.” DNV GL as a classification society offers the unique advantage of providing not only drone-based visual and thickness inspections but also the know-how and experience to interpret the data: “We know the ship, and as surveyors we know exactly what we are looking for,” says Tomasz Oledzki. “We not only take pictures or measurements but we are competent to assess them and confirm the good condition of the ship, and we take responsibility for every aspect of these services. We provide one-stop shopping to owners.”
- Mickael Brock/AMI Studio