Advanced data analytics deliver real-time insights
LNG carriers and other natural gas installations require constant monitoring and proactive maintenance to ensure safe and reliable operation. Digitalization provides the means to accomplish that, and comprehensive data-processing services can extract actionable insights from monitoring data.
Around the world the infrastructure for natural gas production, processing, transport and distribution continues to evolve rapidly. While natural gas will not solve the climate crisis, it is a valuable transitional energy form that mitigates many environmental challenges as man strives to develop true “green” energy forms for a carbon-neutral future. Among the proposed solutions is the large-scale production of hydrogen. Long-term forecasts see hydrogen being produced using electrolysis powered by wind and photovoltaic energy, and its conversion to methane (CH4), which could be distributed using existing natural gas infrastructure. For the time being, hydrogen as an emerging cleaner energy source will primarily result from methane steam reformation of natural gas.
The global natural gas and LNG infrastructure is highly complex, and much of it consists of floating assets, including LNG carriers and floating storage and regasification units (FSRUs), and related equipment. All these vessels carry on-board compressors, expanders, pumps, metering and control devices etc. Monitoring and maintenance play a key role in keeping this infrastructure functional and preventing accidents.
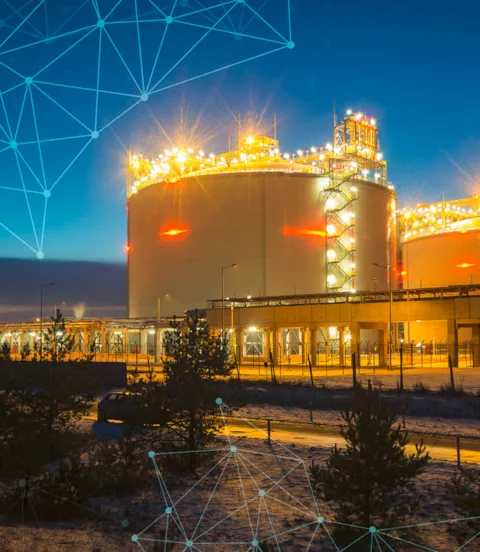
Condition monitoring and predictive maintenance
DNV GL can draw on decades of experience in gas-related engineering and vetting as well as maritime operations, says Chris Dagnall, General Manager of DNV GL’s Rotating Machinery Group. “We have been active in land-based pipeline network monitoring and data acquisition, working closely with customers to provide the insights they need to run their systems smoothly. We know how important it is for a successful condition-monitoring programme to collect and analyse data rapidly so action can be taken promptly. Digitalization allows us to provide automated data analytics solutions covering a wide range of performance-monitoring and maintenance-related needs of asset operators, including real-time reporting.”
Modern ships make use of information and communication technology (ICT) in countless ways, from navigation and routing to equipment monitoring. Through satellite and long-distance wireless connections they are in constant contact with the Internet and their operators’ computer networks, sending and receiving data that ensure smooth operation. Furthermore, on new ships critical equipment is fitted with numerous sensing devices which feed a constant stream of operational data to the ship’s central computer system and data centres on land. All this data harbours tremendous potential for improved decision-making, performance enhancements and condition-based maintenance. Aggregating, correlating and evaluating this data while keeping it safe is a challenging task, however. This is where DNV GL offers its expert support to operators.
Digitalization provides the means to manage complexity by automating rule-based evaluation of large amounts of data that would otherwise require enormous human effort. What is more, data can be interpreted for many different purposes, and the results made available in a cloud environment where they are both well protected and accessible to multiple stakeholders with appropriate access rights. Furthermore, this data can be viewed on a variety of devices and platforms, such as PCs, tablets and smartphones.
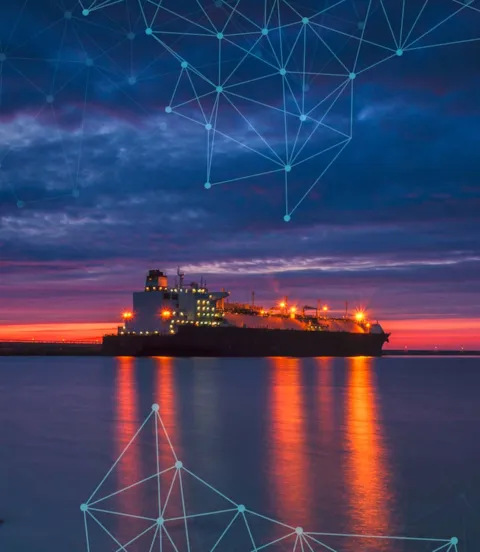
Simulation enables machine reliability improvements
The “digital twin” principle has gained ground rapidly in many industries in recent years. The virtual model of an asset, whether a single piece of equipment or an entire ship, allows its designers and operators to simulate various scenarios to predict the behaviour in well-defined operating conditions. Comparing these operational expectations with actual performance data is an excellent way to identify potential or actual problems, especially when the comparison can itself be automated to deliver rapid results.
In fact, speed is a key factor in all this: the provision of performance, vibration, load and other data to a centralized processing system in near-real time enables quick analysis and reporting so action can be taken promptly. In some cases even this step can be automated so that an equipment manufacturer is notified directly by the software about the equipment’s unexpected behaviour or early signs of a component failure. Where more complex, interdependent systems are under scrutiny, human intervention can be initiated in response to software-generated condition reports delivering solid information.
“DNV GL has been providing these equipment data monitoring, analytics and reporting services to many customers, especially where the equipment being monitored is highly safety-relevant, such as on LNG carriers and FSRUs,” explains Dagnall. “We can install data acquisition hardware on a vessel and receive a full set of performance data sampled at regular time intervals, such as every 10 seconds, in an automated daily transmission to our Veracity platform. All operational data is then analysed using algorithms developed by DNV GL, correlated with vibration data, and assessed to extract key performance indicators and detect any deviations from the predicted performance.”
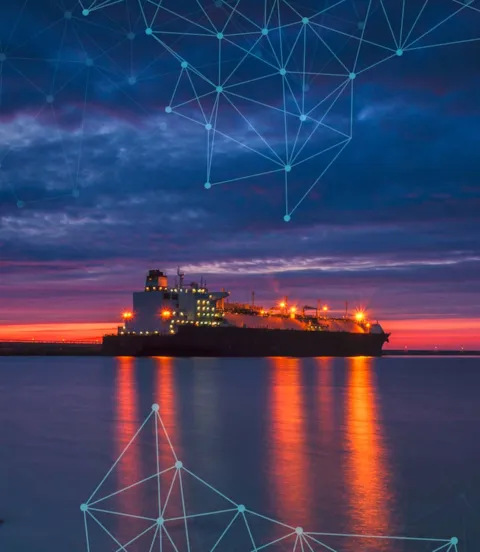
Centralized database accessible from anywhere
The automated reports and notifications generated from the Veracity database can be used for remote fault diagnostics, maintenance decisions, reliability reporting including mean time between failures (MTBF), mean time to repair (MTTR) and availability, as well as asset life tracking, cost tracking, and emissions monitoring and reporting. When an issue has been detected, the operator can take action to address the problem immediately, for example by scheduling corrective measures at the next suitable port stay, routine inspection, dry-docking or other opportunity. Any spare parts needed can be ordered in time so they will be waiting when the ship arrives in port. This avoids unexpected downtime and the associated costs.
Key aspects that make this service effective as well as efficient are the aggregation of the data in a single database and processing system which can provide the most comprehensive insights into the operational condition of a ship, and the ability to access the processed data from any location. This means that owners and operators have a much more solid informational basis for maintenance planning, prioritization and scheduling so they can run their fleets more efficiently and assess the effectiveness of their reliability programmes.
“The value of this data goes far beyond the individual ship,” says Dagnall. “Being able to merge fleet-wide data or even aggregated, anonymized data from multiple vessels and fleets in a single platform allows us to provide the shipping community with a general source of reference information that can be useful in optimizing ship operations, e.g. through reliability, efficiency or emissions benchmarking.” Digitalization thus greatly enhances condition and performance monitoring and analysis and lets all stakeholders involved in the operation of a vessel, whether on board or on shore, access real-time information directly to make well-informed decisions towards improving efficiency and compliance, and reducing costs.
Christopher Charles Dagnall
General Manager - Rotating Machinery Gro
- Key image - ©Wojciech Wrzesien_stock.adobe.com, designed by rawpixel.com/freepik
- Side image 2 - Mike Mareen – Shutterstock.com, designed by rawpixel.com/freepik
- Side image 3 - Wojciech Wrzesien – Shutterstock.com, designed by rawpixel.com/freepik
- Text image - Igor Kardasov – Shutterstock.com