A pioneer in fuel gas technologies
The German engineering contractor TGE Marine is a leading innovator in the dynamic gas carrier business. A pioneer in the development of LNG fuel gas storage and handling systems, TGE was among the first suppliers of advanced LNG fuel gas bunkering systems to meet the needs of the emerging low-emission ship fuel market.
“In the long term, LNG along with methanol will play the leading role as a fuel for marine applications,” says Manfred Küver, CEO at TGE Marine. An engineering firm with more than 30 years’ experience, the company is a main contractor for the growing cryogenic gas market specializing in cargo handling systems and tanks for LPG, LEG, ethane and LNG carriers. In autumn 2015 the Japanese industrial corporation Mitsui Engineering & Shipbuilding (MES) acquired a controlling stake in TGE Marine. “There will be synergies and we believe the two companies will be able to establish an excellent position in the global gas carrier market,” Küver says. Together the two companies can offer turnkey solutions for two-stroke, dual-fuel main engines (under MAN ME-GI licence), including LNG fuel gas systems, as well as specific designs for small LNG carriers.
A promising future market Küver especially sees in small scale LNG: tankers with up to 80,000 m3, LNG bunker vessels and floating storage and regasification units (FSRU). “In view of the environmental regulations more and more owners are looking at gas as a fuel.” With the growing number of new vessel projects specifying dual-fuel engines, the long-anticipated market for small-scale LNG – including bunkering services as well as delivery in small-capacity vessels – is picking up speed.
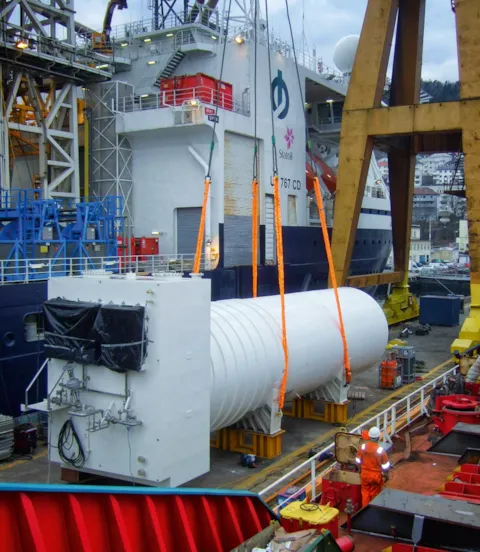
Healthy demand for LNG storage tanks
In early 2016 TGE Marine was granted a European patent for a high-pressure LNG fuel gas system. The TGE engineering team had closely cooperated with Cologne University (TH Köln) on the development of a control system capable of handling the high-speed load profiles imposed by two-stroke dual-fuel main engines running LNG as a primary fuel. The control system was thoroughly tested on board the world’s largest Qmax LNG Carrier Rasheeda owned by Nakilat, a Qatari shipping company.
The system has already been ordered for various newbuilds, among them two 26,500 dwt con-ro vessels contracted in the US by Crowley Maritime Corporation, which will be built by shipyard VT Halter Marine. The vessels will operate in the Caribbean and are among the larger projects in the market. Each vessel will be equipped with three 770 m3 vacuum-insulated LNG storage tanks. TGE will also supply high-pressure/ low-pressure pumps, BOG compressors, vaporizers, a utility and safety system as well as a control and alarm board. Both vessels will be classified by DNV GL and are being built to DNV GL ship class rules as well as USCG regulations. Many other contracts underline TGE Marine’s leading market position. For example, the company was contracted by Jiangnan Shipyard to supply gas handling systems and cargo tanks for four 21,000 m3 liquefied ethylene gas (LEG) carriers for Petredec as well as four 22,000 m3 liquefied petroleum gas (LPG) carriers for Navigator Gas. All vessels are classified by DNV GL.
Another milestone was reached in early May 2016 when AIDA Prima, the world’s first cruise ship to feature a dual-fuel engine capable of running on LNG when docked in port, successfully passed the LNG bunkering test in Hamburg.
TGE delivered the complete LNG fuel system for Aida Prima. A tank truck delivers the LNG to the vessel while in port. This is nothing new, says Küver. LNG-powered ferries and small offshore vessels have been bunkering using LNG trucks for some time, mainly in Norway. The difference is that the AIDA Prima is not “tanked” but the gas is continuously pumped on board all the time the vessel is in port. “Our system complies with all regulations and is extremely safe,” says Küver. The challenge is the procedures and receiving port authority approvals as there are no standard guidelines yet. Separate agreements have to be made with each individual port. DNV GL also supported the owner to be able to carry out the LNG supply at different ports.
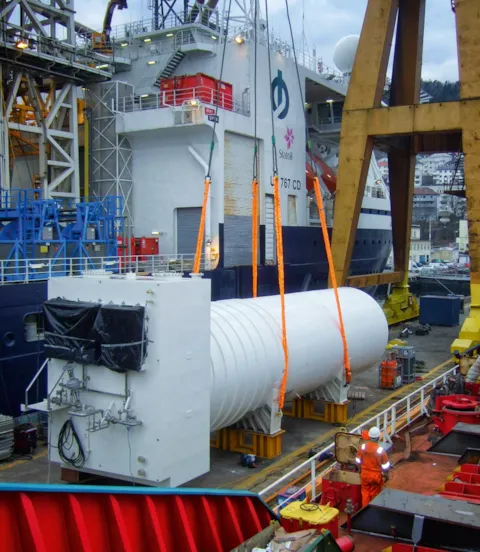
Ensuring safety for gas handling systems
AIDA Prima was built by Mitsubishi Heavy Industries and is classified by DNV GL. The vessel is 300 metres long and 37.6 metres wide, has an eight-metre draught and a gross tonnage of 124,500 tonnes. She is fitted with three MaK 12V M43C main engines and one MaK M46DF dual-fuel marine engine. Key to realizing the Aida projects was TGE’s participation in the GasPax research project between 2010 and 2013. The project partners, of which one was AIDA Cruises, set out to examine the technical challenges associated with the use of LNG in three types of passenger vessels: a Megayacht (Lürssen), a cruise ship (Meyer Werft) and a ro-pax ferry (FSG), and to come up with ready-for market designs.
TGE designed the gas fuel systems for all of the GasPax project vessels. DNV GL was responsible for all class and safety aspects within these projects and issued approval-in-principle certificates for all designs. The project results directly influenced the development of international regulations as well as various ship design projects.
As an expert in gas handling systems, TGE has been actively involved in the development of the latest amendments to the International Code for the Construction and Equipment of Ships Carrying Liquefied Gases in Bulk (IGC), which entered into force on 1 July 2016. The amendments have also been adapted by the International Code of Safety for Ships using Gases or other Low-flashpoint Fuels (IGF), which was adopted by IMO in June 2015. “We presented a strong case for the inclusion of type C tanks as used in the GasPax designs in both codes. Type C tanks have acquired an excellent safety record in the gas tanker market over the years,” says Küver. Thanks to its fail-safe design criteria, Type C is the only tank technology for marine LNG applications which does not require a secondary barrier to minimize the risk of LNG leakage. It thus complies with all applicable safety requirements and is significantly less expensive than vacuum-insulated double-walled tanks.
In terms of safety, Manfred Küver says, the requirements for “tank connection spaces” for type C tanks represent the most advanced development level yet. The fuel containment system shall be so designed that a leak does not endanger the ship, persons on board or the environment. The entire system is double-walled, and all tank connections, fittings, flanges and tank valves must be enclosed in gas-tight tank connection spaces unless the tank connections are located on open deck. The space shall be able to safely contain leakage from the tank in case of leakage from the tank connections. “Another crucial new feature of both codes is the goal-based approach,” says Küver. “Earlier approaches were primarily of a prescriptive nature. The new, goal-based approach provides enough space for new concepts, innovation and improvements.”